Quiz: AME Unit 1 Q4
Next Study Notes:AME Unit 1 Q5
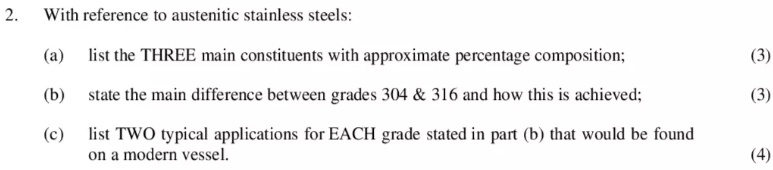
With reference to austenitic stainless steels:
(a) list the THREE main constituents with approximate percentage composition; (3)
(b) state the main difference between grades 304 & 316 and how this is achieved; (3)
(c) list TWO typical applications for EACH grade stated in part (b) that would be found on a modern vessel.
(a) list the THREE main constituents with approximate percentage composition; (3)
Three Main Constituents of Austenitic Stainless Steel
Austenitic stainless steels primarily consist of:
- Iron (Fe): As the base metal, iron constitutes the majority of the alloy, typically around 65-75%.
- Chromium (Cr): This element is essential for providing corrosion resistance, typically present at 16-26%.
- Nickel (Ni): Contributing to the austenitic structure and enhancing corrosion resistance, nickel content ranges from 8-35%.
Note: While these are the primary elements, other elements like manganese, silicon, and carbon are also present in smaller quantities and influence the specific properties of the stainless steel.
(b) state the main difference between grades 304 & 316 and how this is achieved; (3)
Difference Between Grade 304 and 316 Stainless Steel
The primary distinction between Grade 304 and 316 stainless steel is their corrosion resistance.
- Grade 304 is a widely used austenitic stainless steel recognized for its good corrosion resistance.
- Grade 316 is also an austenitic stainless steel, but it offers superior corrosion resistance, particularly in chloride environments.
This enhanced corrosion resistance in Grade 316 is attributed to the addition of molybdenum. Molybdenum significantly improves the steel’s resistance to pitting and crevice corrosion, making it suitable for marine applications, chemical processing, and food processing industries where exposure to chlorides is common.
What is Molybdenum?
Molybdenum
Molybdenum is a chemical element with the symbol Mo and atomic number 42. It is a silvery-grey metal renowned for its exceptional strength, hardness, and resistance to extreme temperatures.
Key Properties
- High melting point
- Excellent strength and hardness
- Corrosion resistance
- Low coefficient of thermal expansion
Uses
Molybdenum is primarily used in the production of alloys. Its addition to steel significantly enhances its strength, toughness, and resistance to wear and corrosion. It is also used in:
- Superalloys
- Pigments
- Catalysts
- Lubricants
Molybdenum is also an essential trace element for plants and animals, playing a crucial role in various biological processes.
Opens in a new windowen.wikipedia.org
molybdenum
Resources:
WebMD: https://www.webmd.com/vitamins/ai/ingredientmono-1249/molybdenum
Royal Society of Chemistry: https://www.rsc.org/periodic-table/element/42/molybdenum
Britannica: https://www.britannica.com/science/molybdenum
Where do you find molybdenum in diesel engines?
Molybdenum in Diesel Engines
Molybdenum plays a crucial role in enhancing the performance and durability of diesel engines. It is primarily found in the following components:
Engine Components with Molybdenum
- Engine oils: Molybdenum-based additives are commonly used in diesel engine oils to reduce friction, wear, and deposit formation. These additives form a protective layer on metal surfaces, improving engine efficiency and extending oil life.
- Piston rings: Molybdenum coatings or alloys can be applied to piston rings to enhance their durability and reduce friction. This helps to improve engine performance and fuel economy.
- Valve components: Molybdenum-containing alloys can be used in valve components to improve their resistance to wear and corrosion, ensuring optimal engine performance.
- Other engine components: Molybdenum may also be present in other engine components, such as bearings and gears, to enhance their performance and longevity.
By incorporating molybdenum into various engine components, diesel engine manufacturers can improve engine efficiency, reduce emissions, and extend engine life.
(c) list TWO typical applications for EACH grade stated in part (b) that would be found on a modern vessel.
Two Typical Applications for 304 Stainless Steel in Marine Applications
Interior Components: In marine vessels, 304 stainless steel is often used for interior components like sinks, countertops, and decorative elements. Its hygienic properties and resistance to corrosion make it suitable for these applications.
Deck Equipment: 304 stainless steel is commonly used for deck fittings and equipment due to its good corrosion resistance and aesthetic appeal. This includes items such as handrails, railings, ladders, and other components exposed to the marine environment.
Two Typical Applications for 316 Stainless Steel in Marine Applications
Marine Piping Systems: 316 stainless steel is widely used in marine piping systems due to its excellent corrosion resistance, especially in saltwater environments. It’s commonly used for pipes, fittings, and valves that transport seawater, freshwater, and other fluids within a vessel.
Deck Hardware: Given its strength, durability, and corrosion resistance, 316 stainless steel is a popular choice for deck hardware. This includes railings, handrails, cleats, hinges, and other fittings exposed to the harsh marine environment.
When to Use 316 Instead of 304 Stainless Steel in Marine Environments
While both 304 and 316 stainless steels offer good corrosion resistance, 316 is specifically designed to withstand harsher conditions, particularly those with high chloride content. Here are some specific examples:
1. 304 vs 316 Stainless Steel: What You Need to Know
1. Components Exposed to Saltwater Spray or Immersion:
- Boat hulls and superstructures: Areas subjected to constant saltwater exposure, such as the lower part of a boat hull or superstructures in coastal regions.
- Marine equipment: Components like winches, anchors, and chain lockers that are frequently exposed to saltwater.
2. Components in Enclosed Spaces with High Humidity and Salt Air:
- Bilge pumps and systems: These components operate in environments with high humidity and potential exposure to saltwater, making 316 a better choice for long-term durability.
- Marine plumbing systems: Pipes, fittings, and valves in marine plumbing systems can be exposed to saltwater or brackish water, requiring the superior corrosion resistance of 316.
3. Components Subjected to Chemical Exposure:
Wastewater systems: Components in contact with wastewater, which often contains salts and other corrosive substances, benefit from the increased corrosion resistance of 316.
Chemical tanks and equipment: If a marine vessel handles chemicals, especially those containing chlorides, 316 stainless steel is essential to prevent corrosion.