Quiz: AME Unit 1 Q5
Next Study Notes:AME Unit 1 Q6
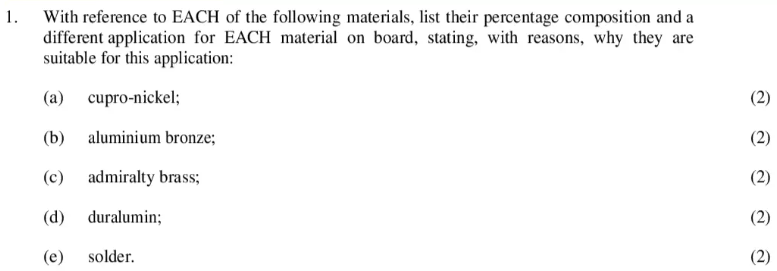
With reference to EACH of the following materials, list their percentage composition and a different application for EACH material on board, stating, with reasons, why they are suitable for this application:
(a) cupro-nickel;(2)
(b) aluminium bronze;(2)
(c) admiralty brass;(2)
(d) duralumin;(2)
(e) solder.(2)
What is cupro-nickel?
Cupro-nickel
is an alloy primarily composed of copper and nickel. Its composition typically ranges from 60 to 90% copper and 10 to 40% nickel. Other elements can be added in small quantities to enhance specific properties.
This alloy is renowned for its excellent corrosion resistance, especially in saltwater environments. It also offers good thermal conductivity and mechanical properties.
Copper Nickel Alloys (CuNi): Definition, Applications, Advantages, and Disadvantages
Cupro-nickle marine applications
Composition:
- Primarily copper (Cu), typically 70-90%
- Nickel (Ni), constituting the remaining percentage (10-30%)
Application:
Heat Exchanger Tubes: Cupro-nickel alloys are widely used for heat exchanger tubes in marine vessels.
Ship Hulls: Cupro-nickel alloys, particularly those with higher copper content, can be used for ship hulls.
Reason: The inherent antifouling properties of copper, combined with the corrosion resistance of nickel, make cupro-nickel hulls less susceptible to marine organism attachment, reducing drag and improving fuel efficiency. Additionally, the alloy’s strength and durability contribute to the overall hull integrity.
What is aluminium bronze?
Aluminium Bronze
Aluminium bronze is a copper-based alloy where aluminium is the primary alloying element.
Typically, it contains 5-11% aluminium, with the remaining composition being copper.Other elements like iron, nickel, manganese, and silicon can be added to enhance specific properties.
Known for its high strength, excellent corrosion resistance, and wear resistance, aluminium bronze is widely used in various industries, including marine applications.
1. What Is Aluminum Bronze? | Aluminum Bronze Alloy – MetalTek International
Aluminium Bronze Marine Applications
Aluminium bronze is widely used in marine applications due to its exceptional corrosion resistance, strength, and durability. Here are some common examples:
- Propellers: The combination of strength, corrosion resistance, and erosion resistance makes aluminium bronze an excellent choice for ship propellers, especially in challenging marine environments. 1. Aluminum Bronzes – Copper Development Association copper.org
- Valve components: Due to its resistance to wear, corrosion, and cavitation, aluminium bronze is used for valve seats, stems, and other critical components.
- Pump impellers: The material’s ability to withstand abrasive and corrosive conditions makes it ideal for pump impellers, ensuring efficient and long-lasting operation.
- Shafts and bearings: Aluminium bronze offers excellent wear resistance and fatigue strength, making it suitable for shafts and bearings in marine machinery.
These applications highlight the versatility of aluminium bronze and its ability to perform reliably in the demanding marine environment.
What is Admiralty Brass?
Admiralty brass is a type of brass alloy primarily composed of copper, zinc, and a small amount of tin.
Its typical composition is approximately 70% copper, 29% zinc, and 1% tin.
This alloy is specifically designed for its excellent corrosion resistance, especially in marine environments. The addition of tin helps to inhibit dezincification, a type of corrosion that can affect brass.
Marine Applications of Admiralty Brass
Admiralty brass is renowned for its exceptional corrosion resistance, making it a prime choice for numerous marine applications.
Here are some common examples:
- Heat Exchanger Tubes: Admiralty brass is extensively used in heat exchangers due to its excellent thermal conductivity and resistance to seawater corrosion. Its ability to efficiently transfer heat while maintaining structural integrity is crucial in marine cooling systems.
- Condenser Tubes: Similar to heat exchangers, condensers in marine systems often employ Admiralty brass tubes to withstand the corrosive environment and facilitate efficient heat transfer.
- Seawater Piping: Due to its resistance to saltwater, Admiralty brass is suitable for piping systems that handle seawater in marine vessels.
- Marine Hardware: While less common than other brass alloys in this application, Admiralty brass can be used for certain marine hardware components where superior corrosion resistance is required.
The combination of high corrosion resistance, good thermal conductivity, and suitable mechanical properties makes Admiralty brass a valuable material for various marine components.
1. An Expert’s Guide to Admiralty Brass Tubes – Munot Metalloys
What is Duralumin?
Duralumin is a trade name for one of the earliest types of age-hardenable aluminum-copper alloys. It’s a combination of the words “Dürener” (referring to the company that initially produced it) and “aluminum”.
Key characteristics:
- Age-hardenable: It gains strength through a heat treatment process.
- Light weight: Significantly lighter than steel.
- High strength: Offers good strength-to-weight ratio.
- Ductility: Can be easily formed into various shapes.
Modern equivalent: The term duralumin is now obsolete. The modern equivalent of duralumin is the 2000 series of aluminum alloys, such as 2014 and 2024, which offer similar properties.
Duralumin | Aluminum-Copper, Strength & Durability – Britannica www.britannica.com
Duralumin – Chemical Composition, Mechanical Properties and Common Applications www.azom.com
1. What is the use of duralumin and its composition ? – BYJU’S byjus.com
Marine Applications of Duralumin (or Modern Equivalents)
While duralumin itself is obsolete, its modern equivalents, primarily the 2000 series aluminum alloys, find various applications in the marine industry.
Due to their high strength-to-weight ratio, these alloys were once popular for:
- Aircraft components: Although not strictly marine, the technology and materials developed for aircraft often found applications in marine vessels.
- High-performance boat hulls: For racing or high-speed vessels where weight reduction is crucial, these alloys could be used in specific components.
However, it’s important to note:
- Corrosion resistance: Duralumin and its successors have limited corrosion resistance in marine environments. This restricts their use in direct contact with seawater. 1. Marine Applications of Aluminum Alloys: Part One | Total Materia www.totalmateria.com
- Modern alternatives: Modern aluminum alloys, particularly the 5000 and 6000 series, offer superior corrosion resistance and are more commonly used in marine applications today.
While duralumin and its derivatives once had potential in marine applications, the advancements in aluminum alloy technology have led to the preference for other alloys that better suit the demanding marine environment.
Modern Aluminum Alloys in Marine Applications
While duralumin has been superseded, the aluminum alloy family offers numerous options for marine applications. Let’s explore some common alloys and their uses:
5000 Series Aluminum Alloys
- Composition: Primarily aluminum and magnesium.
- Characteristics: Excellent corrosion resistance, good weldability, and moderate strength.
- Applications: Hulls, decks, superstructures, and other structural components due to their corrosion resistance and formability.
6000 Series Aluminum Alloys
- Composition: Aluminum, magnesium, and silicon.
- Characteristics: Good strength, excellent weldability, and moderate corrosion resistance.
- Applications: Frames, beams, and other structural elements where strength and weldability are essential.
Other Notable Alloys
- 4000 Series: Offers good castability and wear resistance, suitable for engine blocks and pump impellers.
- 7000 Series: Known for high strength but typically not used extensively in marine applications due to lower corrosion resistance compared to 5000 and 6000 series.
Key considerations for selecting aluminum alloys in marine environments:
Formability: The ability to form the alloy into desired shapes is important for various components.
Corrosion resistance: The marine environment is highly corrosive, so choosing alloys with good corrosion resistance is crucial.
Strength-to-weight ratio: Aluminum alloys offer excellent strength-to-weight ratios, making them ideal for weight-sensitive applications.
Weldability: Many marine components require welding, so choosing a weldable alloy is essential.
What is solder?
Solder is a fusible metal alloy used to create a permanent bond between metal workpieces. It has a lower melting point than the metals being joined, allowing it to melt and flow into the joint, creating a strong connection when it cools.
Solder is typically composed of a mixture of metals, such as tin and lead (though lead-free solders are increasingly common due to environmental concerns). The specific composition determines the solder’s melting point and other properties.
Key characteristics of solder:
- Low melting point
- Good electrical conductivity
- Good thermal conductivity
- Ductility
Solder is widely used in electronics, plumbing, and other industries for joining metal components.
Marine Applications of Solder
While soldering is a common technique in many industries, its application in marine environments is specific and often limited due to the harsh conditions. However, there are a few key areas where solder is used:
1. Electrical Connections:
- Small-scale connections: Solder is used to create electrical connections in marine electronics, such as radios, fish finders, and other devices. However, it’s crucial to use high-quality, marine-grade solder and ensure proper insulation to prevent corrosion and electrical failures.
- Repairing broken wires: Solder can be used to repair broken wires in marine electrical systems, but it’s essential to consider the long-term durability of the joint in a damp environment.
2. Plumbing and Pipe Fitting:
- Soft solder: In some cases, soft solder might be used for low-pressure water systems or non-critical plumbing connections. However, it’s important to note that brazing or welding is generally preferred for most marine plumbing due to the higher strength and durability requirements.
3. Fishing Equipment:
- Sinkers and weights: Solder is used to attach weights to fishing lines and lures.
- Bait and tackle repair: It can be used to repair damaged fishing equipment.
Important Considerations:
- Corrosion: The marine environment is highly corrosive. Therefore, it’s crucial to use marine-grade solder and protective coatings to prevent corrosion of the soldered joints.
- Vibration: Marine environments are subject to vibrations. The soldered joints must be mechanically sound to withstand these vibrations.
- Temperature extremes: Solder joints should be able to withstand the temperature variations typical of marine environments.
In conclusion, while solder has some applications in marine environments, its use is often limited due to the harsh conditions. For most critical connections, alternative methods like brazing, welding, or crimping are preferred.
1. Corrosion Resistance in Marine Environments – Marsh Fasteners www.marshfasteners.com
2. A Solder Guide for Bait and Tackle and Marine Uses – Mayer Alloys mayeralloys.com