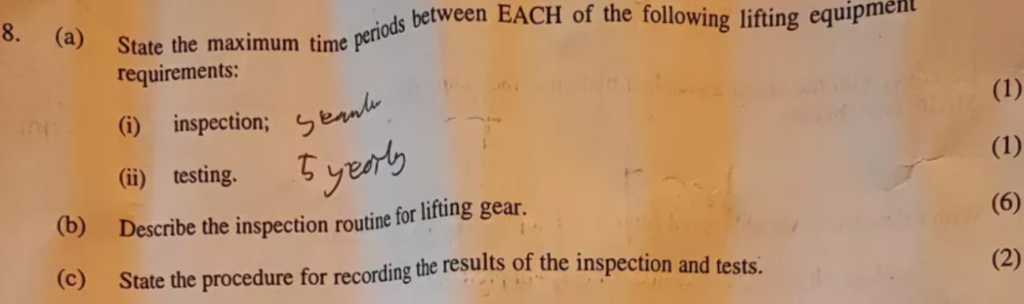
(a) State the maximum time periods between EACH of the following lifting equipment requirements:
(i) inspection;
(ii) testing.
(b) Describe the inspection routine for lifting gear.(6)
(c) State the procedure for recording the results of the inspection and tests.(2)
Inspections of lifting equipment requirements
The maximum time periods between inspections of lifting equipment vary depending on the type of equipment and its usage, but generally follow these guidelines as outlined in the Lifting Operations and Lifting Equipment Regulations 1998 (LOLER):
- 6 Months:
- Lifting equipment and any associated accessories used to lift people.
- All lifting accessories (e.g., slings, shackles, hooks).
- 12 Months:
- All other lifting equipment not used to lift people.
It’s important to emphasize that these are the maximum intervals.
- More Frequent Inspections: In some cases, more frequent inspections may be necessary. This depends on the equipment’s condition, frequency of use, and the operating environment. The equipment manufacturer’s recommendations should also be considered.
- Competent Person: All inspections must be carried out by a competent person who has the knowledge and experience to identify defects and assess the equipment’s safety.
Beyond Inspections: Thorough Examinations
In addition to regular inspections, lifting equipment must also undergo a more comprehensive thorough examination at specific intervals:
- Lifting equipment and any associated accessories used to lift people: Every 6 months
- All other lifting equipment: Every 12 months
This examination is more in-depth and may involve dismantling parts, non-destructive testing, and load testing.
Key Takeaway:
Regular inspections and thorough examinations are crucial for ensuring the safety and reliability of lifting equipment. By adhering to these requirements and following the manufacturer’s recommendations, operators can minimize the risk of accidents and maintain a safe working environment.
Testing of lifting equipment requirements
The maximum time periods between testing of lifting equipment, as per the Lifting Operations and Lifting Equipment Regulations 1998 (LOLER), are:
- 6 Months:
- Lifting equipment used to lift people.
- All lifting accessories (e.g., slings, shackles, hooks).
- 12 Months:
- All other lifting equipment not used to lift people.
These are the maximum intervals allowed, and more frequent testing may be necessary depending on factors such as:
- Manufacturer’s recommendations
- Frequency of use
- Operating conditions
- Results of previous inspections
Remember, the testing must always be carried out by a competent person.
Inspection routine for lifting gear
The inspection routine for lifting gear, as outlined in the Code of Safe Working Practices for Merchant Seafarers (COSWP) and other relevant regulations, involves a combination of pre-use checks, regular inspections, and thorough examinations.
1. Pre-Use Checks:
- Visual Inspection: Before each use, the operator should conduct a visual inspection of the lifting gear, looking for any obvious signs of damage, wear, or defects.
- Functional Checks: Test the operation of any moving parts, such as hooks, shackles, or release mechanisms, to ensure they function smoothly and correctly.
- Check Markings and Labels: Verify that all markings and labels, including SWL/WLL, identification numbers, and any safety warnings, are clear and legible.
2. Regular Inspections:
- Frequency: The frequency of regular inspections depends on the type of equipment, usage, and operating environment. Generally, lifting accessories should be inspected at least every 6 months, while other lifting equipment should be inspected at least every 12 months.
- Scope: These inspections are more detailed than pre-use checks and may involve closer examination of components, checking for wear and tear, lubrication, and basic functional tests.
3. Thorough Examinations:
- Frequency: Thorough examinations are more comprehensive inspections typically carried out annually or at intervals specified by regulations or the manufacturer.
- Scope: They may involve dismantling parts, non-destructive testing (NDT), and load testing to assess the equipment’s overall condition and identify any hidden defects or weaknesses.
- Competent Person: Thorough examinations must be conducted by a competent person with the necessary knowledge and experience in lifting equipment inspection and testing.
Specific Items to Inspect:
The inspection routine should cover all parts of the lifting gear, including:
- Chains and Slings: Check for wear, elongation, cracks, deformation, or damage to links or hooks.
- Wire Ropes: Inspect for broken wires, kinks, corrosion, or reduction in diameter.
- Hooks and Shackles: Check for cracks, deformation, wear in the throat opening, and proper operation of safety latches.
- Blocks and Pulleys: Inspect for wear on sheaves and bearings, cracks, and proper function of swivels.
- Spreader Beams and Lifting Beams: Check for cracks, deformation, and secure attachment of lifting lugs or shackles.
- Other Accessories: Inspect any other lifting accessories, such as eyebolts, turnbuckles, or clamps, for signs of wear, damage, or corrosion.
Record Keeping:
- Maintenance and Inspection Records: Maintain detailed records of all inspections, maintenance, repairs, and thorough examinations. Include dates, findings, and any corrective actions taken.
- Certification: Keep copies of all relevant certificates, such as proof load test certificates and inspection reports.
Key Points:
- Prioritize Safety: The primary goal of the inspection routine is to ensure the safety of personnel and prevent accidents during lifting operations.
- Follow Recommendations: Adhere to the manufacturer’s instructions and any relevant regulations regarding inspection and maintenance intervals.
- Competent Personnel: Use qualified and experienced individuals to conduct inspections and examinations.
- Timely Repairs: Address any identified defects or issues promptly to prevent further deterioration and ensure the equipment’s continued safe use.
By implementing a rigorous inspection routine and adhering to best practices, vessel operators can maintain the integrity and safety of their lifting gear, minimizing risks and ensuring efficient and compliant lifting operations.
Procedure for recording the results of the inspection and tests.
The procedure for recording the results of inspections and tests for lifting equipment should be systematic, detailed, and compliant with relevant regulations like LOLER. Here’s a general outline:
1. Use a Dedicated Record Book or System:
- Logbook: A physical logbook specifically for lifting equipment inspections and maintenance is often used.
- Digital System: Alternatively, a computerized maintenance management system (CMMS) or a dedicated software can be utilized to store and manage these records electronically.
2. Include Essential Information for Each Entry:
- Equipment Identification: Unique identifier (e.g., serial number, tag number) to clearly identify the specific piece of equipment.
- Date of Inspection/Test: The exact date when the inspection or test was conducted.
- Type of Inspection/Test: Specify whether it was a pre-use check, regular inspection, or thorough examination.
- Name of Competent Person: Record the name and signature of the person who conducted the inspection or test, ensuring they are qualified and competent.
- Findings and Observations: Clearly document the results of the inspection or test, including:
- Condition of the equipment: Note any wear, damage, defects, or other observations about the equipment’s condition.
- Measurements and Test Results: Record any measurements taken, such as wire rope diameters, chain link dimensions, or load test results.
- Functional Checks: Note the results of any functional tests performed on controls, safety devices, or alarms.
3. Action Taken:
- Repairs or Replacements: If any defects or deficiencies were identified, detail the corrective actions taken, such as repairs, replacements, or adjustments.
- Next Inspection Date: Specify the date for the next scheduled inspection or examination.
4. Additional Information:
- Attachments: Attach any relevant supporting documents, such as photographs of defects, NDT reports, or certificates of compliance.
- Comments: Include any additional comments or observations that may be relevant for future reference or analysis.
5. Retention and Accessibility:
- Secure Storage: Ensure the records are securely stored and protected from loss or unauthorized alteration.
- Easy Access: The records should be readily accessible to authorized personnel, such as the ship’s officers, engineers, and safety representatives, as well as any regulatory inspectors or auditors.
Specific Requirements:
- LOLER: The Lifting Operations and Lifting Equipment Regulations 1998 (LOLER) mandate that inspection and thorough examination records be kept for at least two years for lifting equipment and accessories used to lift people, and for at least five years for all other lifting equipment.
- Classification Society Rules: Classification societies may have additional requirements for record-keeping, including specific formats or information to be included in the records.
Benefits of Proper Record Keeping:
- Safety: Helps ensure the ongoing safety and reliability of lifting equipment by tracking its condition, maintenance history, and compliance with regulations.
- Traceability: Provides a clear history of inspections and maintenance, allowing for traceability and accountability in case of any incidents or accidents.
- Maintenance Planning: Helps plan future maintenance and repairs, ensuring that equipment is serviced at appropriate intervals.
- Regulatory Compliance: Demonstrates compliance with LOLER and other relevant regulations, avoiding potential penalties or detentions.
Conclusion:
Properly recording the results of inspections and tests is an integral part of a safe and effective lifting equipment management system. By maintaining accurate and comprehensive records, ship operators can ensure the ongoing safety and compliance of their lifting gear, minimize risks, and promote a culture of safety on board.