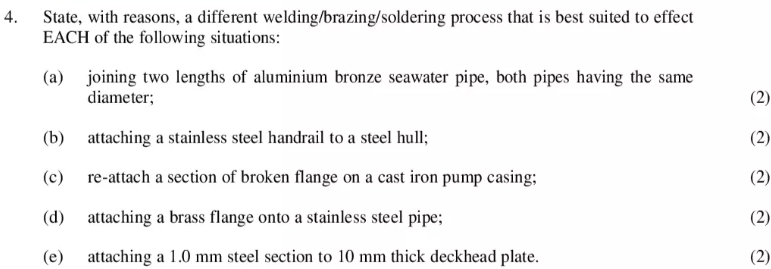
(a) Joining two lengths of aluminum bronze seawater pipe, both pipes having the same diameter.
The best process for this situation is gas tungsten arc welding (GTAW), also known as TIG welding. TIG welding is a precise and controlled process that is well-suited for joining thin materials, such as aluminum bronze. It is also resistant to corrosion, which is important for seawater pipes.
Gas tungsten arc welding (GTAW)
(b) Attaching a stainless steel handrail to a steel hull.
The best process for this situation is shielded metal arc welding (SMAW), also known as stick welding. SMAW is a versatile process that can be used to join a variety of metals, including steel and stainless steel. It is also a relatively inexpensive and portable process, which makes it a good choice for shipboard repairs.
Shielded metal arc welding (SMAW)
(c) Re-attaching a section of broken flange on a cast iron pump casing.
The best process for this situation is brazing. Brazing uses a filler metal that has a lower melting point than the base metals. This allows the filler metal to melt and flow into the joint, without melting the base metals. Brazing is a good choice for cast iron because it is less likely to cause cracking.
Brazing
(d) Attaching a brass flange onto a stainless steel pipe.
The best process for this situation is silver soldering. Silver solder is a type of solder that has a high melting point and is very strong. It is a good choice for joining dissimilar metals, such as brass and stainless steel.
Silver soldering
(e) Attaching a 1.0 mm steel section to 10 mm thick deckhead plate.
The best process for this situation is laser beam welding. Laser beam welding is a high-energy process that can create very strong and narrow welds. It is a good choice for this situation because it can weld the thin steel section to the thicker deckhead plate without melting too much of either metal.