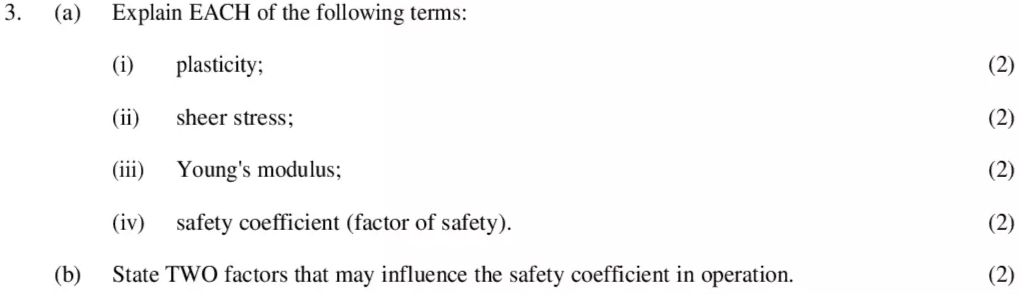
(a) Definitions:
(i) Plasticity:
The property of a material to undergo permanent deformation under stress. Unlike elastic materials that return to their original shape after stress is removed, plastic materials retain a portion of the deformation. Imagine bending a paperclip – it retains the bend after you let go.
(ii) Shear Stress:
The stress that tends to slide or distort one part of a material relative to another along a parallel plane. Picture sliding two books against each other, causing them to shear and potentially tear.
(iii) Young’s Modulus:
Also known as the elastic modulus, it measures the stiffness of a material. It quantifies the relationship between stress and strain within the elastic range (where deformation is temporary). A higher Young’s modulus indicates a stiffer material that requires more force to deform a given amount. Think of a stiff beam compared to a limp noodle.
(iv) Safety Coefficient (Factor of Safety):
A factor applied to the design load of a component to ensure it has sufficient strength to handle actual operating conditions with a buffer against unexpected stresses or material imperfections. It acts as a safeguard against component failure and associated risks. Imagine adding extra bricks to a bridge design to ensure it can safely support cars and trucks.
(b) Factors Influencing Safety Coefficient:
(i) Operating Conditions: Unexpected loads or environmental factors like extreme temperatures, corrosive environments, or sudden shocks can necessitate a higher safety coefficient to account for these additional stresses.
(ii) Material Properties: Variations in material properties due to manufacturing processes, aging, or inherent inconsistencies can require adjusting the safety coefficient to ensure reliable performance despite these uncertainties.