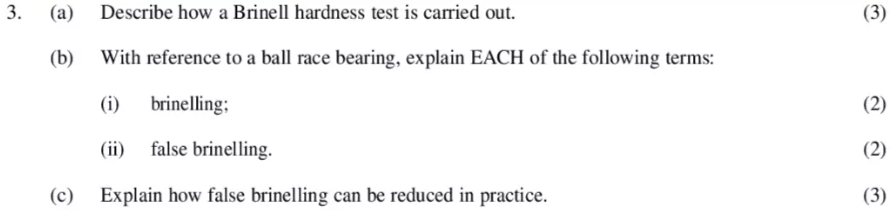
The Brinell hardness test determines the indentation hardness of a material by measuring the permanent impression left by a hardened steel ball pressed into its surface. Here’s how it’s carried out:
- Preparation: The test surface is prepared by polishing and cleaning to ensure accurate testing.
- Test Equipment: A Brinell hardness tester consists of a press capable of applying a specific load, a hardened steel ball (typically 10mm diameter), and a measuring microscope.
- Load Application: The chosen load (based on material and test standard) is applied to the ball in contact with the test surface for a specific dwell time (typically 10-30 seconds).
- Indentation Measurement: The diameter of the indentation left on the surface is measured using a microscope.
- Hardness Calculation: Using the measured diameter, load, and ball diameter, the Brinell Hardness Number (HB) is calculated using a specific formula. Higher HB values indicate higher hardness.
(b) Ball Race Bearing Terms:
(i) Brinelling:
Brinelling is a type of permanent indentation damage on the raceway (tracks) of a ball bearing caused by excessive static or shock loads. These indentations resemble the size and shape of the rolling elements (balls) and can lead to:
- Increased noise and vibration: Uneven rolling due to indentations creates noise and vibration during bearing operation.
- Reduced load capacity: Indentations weaken the raceway, lowering the bearing’s ability to handle loads without failure.
- Premature bearing failure: Repeated stress on the indented areas can lead to cracks and eventual bearing failure.
(ii) False Brinelling:
False brinelling, also known as fretting fatigue, is another type of surface damage that resembles brinelling but arises from different causes. It occurs due to:
- Microscopic vibrations: Slight movement or vibration between stationary rolling elements and the raceway creates wear and micro-cracks.
- Loss of lubrication: Inadequate lubrication allows direct metal-to-metal contact, accelerating wear and fatigue.
- Corrosive environments: Corrosive elements can break down lubricants and promote surface damage.
False brinelling appears as shallow, matte-textured lines or areas along the raceway and can also lead to noise, vibration, and reduced bearing lifespan.
(c) Reducing False Brinelling:
Several practices can reduce the risk of false brinelling in ball race bearings:
- Properly sized and selected bearings: Choosing bearings with adequate load capacity and appropriate materials for the expected loads and environment is crucial.
- Maintaining lubrication: Regular lubrication with the correct type and quantity of grease or oil minimises metal-to-metal contact and protects against corrosion.
- Vibration control: Minimising sources of vibration through proper component design, mounting, and alignment reduces stress on the bearing.
- Surface coating: Applying protective coatings to the raceway and rolling elements can enhance wear resistance and reduce micro-cracking.
- Monitoring and inspection: Regularly monitoring bearing noise, vibration, and temperature helps identify potential false brinelling before significant damage occurs, allowing for preventative maintenance.
By implementing these strategies, the risk of false brinelling can be effectively mitigated, ensuring optimal performance and lifespan for ball race bearings.