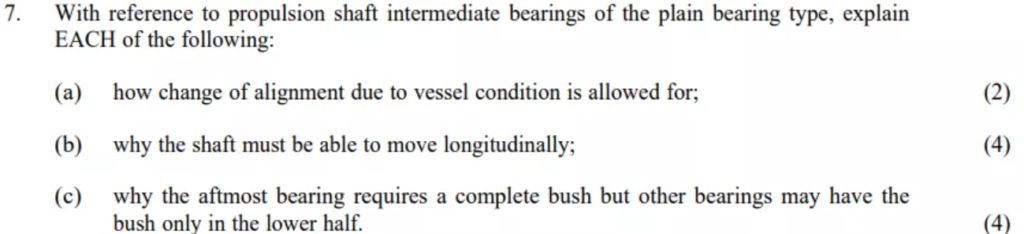
With reference to propulsion shaft intermediate bearings of the plain bearing type, explain EACH of the following:
(a) how change of alignment due to vessel condition is allowed for;(2)
(b) why the shaft must be able to move longitudinally;(4)
(c) why the aftmost bearing requires a complete bush but other bearings may have the bush only in the lower half.(4)
What are propulsion shaft intermediate bearings?
Propulsion shaft intermediate bearings are critical components in a vessel’s power transmission system. They provide support and guidance to the intermediate shaft(s) that connect the main engine or gearbox to the propeller shaft. These bearings help to:
1. Simplex Intermediate shaft bearings – SKF
2. Intermediate Propeller Shaft Bearing | ISB Series – R.E. Thomas Marine Hardware
- Reduce Friction: Minimize friction between the rotating shaft and the stationary bearing housing, ensuring smooth power transmission and reducing energy losses.
- Control Shaft Deflection: Limit the bending and deflection of the intermediate shaft, preventing excessive vibration and stress on the shaft and other components.
- Maintain Alignment: Help maintain proper alignment between the various shaft sections, contributing to efficient power transmission and reduced wear and tear.
- Support Shaft Weight: Support the weight of the intermediate shaft, preventing it from sagging or bending under its own weight and the forces transmitted from the engine.
Types of Intermediate Shaft Bearings
Several types of bearings can be used for intermediate shaft support, each with its own advantages and suitable applications:
- Plain Bearings (also known as Journal Bearings):
- Simple and cost-effective, using a cylindrical sleeve (bearing bush) lined with a low-friction material like white metal (babbitt) or a synthetic polymer.
- Rely on hydrodynamic lubrication, where a film of oil separates the shaft from the bearing surface.
- Suitable for various applications but may require more frequent maintenance and are sensitive to misalignment.
- Tilting Pad Bearings:
- More complex but offer superior load-carrying capacity and self-aligning capability.
- Consist of multiple pads that pivot to accommodate shaft misalignment and maintain an optimal oil film thickness.
- Well-suited for heavy-duty applications and large vessels.
- Roller Bearings:
- Use rolling elements (rollers) between the shaft and bearing housing to reduce friction and handle high loads.
- Offer low friction and good efficiency, especially at low speeds.
- Can be more sensitive to shock loads and require careful installation and maintenance.
Lubrication:
- Oil Lubrication: Most common, with oil being circulated through the bearing housing to provide a lubricating film and remove heat.
- Water Lubrication: Some modern bearings utilize seawater for lubrication, offering environmental benefits by eliminating the risk of oil pollution. 1. Controlling the bearing environment – Riviera Maritime Media www.rivieramm.com
Additional Features:
- Bearing Housings: Provide a secure enclosure for the bearing and facilitate oil or water circulation.
- Seals: Prevent oil leakage or water ingress, depending on the bearing type.
- Cooling Systems: May incorporate cooling systems to remove heat generated by friction.
Importance:
- Efficient Power Transmission: Properly functioning intermediate shaft bearings ensure smooth and efficient power transmission from the engine to the propeller.
- Reduced Wear and Tear: Minimizes friction and wear on the shaft and bearings, extending their lifespan and reducing maintenance costs.
- Vibration Control: Helps control shaft deflection and vibration, enhancing passenger and crew comfort and reducing stress on the vessel’s structure.
- Safety: Reliable bearings prevent shaft failure, which could lead to loss of propulsion and potential safety hazards.
Maintenance:
Regular inspection and maintenance of intermediate shaft bearings are crucial to their performance and longevity. This typically involves checking oil levels and condition, inspecting for wear or damage, and replacing bearings or seals as needed.
By providing crucial support and guidance to the intermediate shaft, these bearings play a vital role in ensuring the efficient and safe operation of the vessel’s propulsion system.
Change of alignment due to vessel condition
Plain bearings, also known as journal bearings, are commonly used as intermediate shaft bearings in marine propulsion systems. While they offer simplicity and cost-effectiveness, they are inherently less tolerant of misalignment compared to other bearing types like tilting pad bearings. However, certain design features and considerations allow them to accommodate some degree of shaft misalignment due to changes in vessel condition.
1. Plain Bearings in Marine Applications | Request PDF – ResearchGate
2. On the Characteristics of Misaligned Journal Bearings – MDPI
1. Bearing Clearance:
- Designed-in Clearance: Plain bearings are designed with a small clearance between the shaft journal (the part of the shaft supported by the bearing) and the bearing surface. This clearance allows for some degree of misalignment without causing excessive friction or binding.
- Oil Film: During operation, a hydrodynamic oil film forms between the shaft and bearing, further accommodating slight misalignment and ensuring smooth rotation.
2. Bearing Material and Design:
- Soft Bearing Material: The bearing shells or bushings are typically made of a soft, conformable material like white metal (babbitt). This allows the bearing surface to conform slightly to the shaft’s position, accommodating minor misalignment.
- Split Bearing Design: Many plain bearings have a split design, with two halves that can be adjusted slightly during installation to compensate for initial misalignment.
3. Flexible Couplings:
- Adjacent to Bearings: Flexible couplings are often installed on the shafting system adjacent to the plain bearings. These couplings can accommodate some degree of angular and axial misalignment, reducing the stress transmitted to the bearings. 1. Keeping an eye on alignment – Plant Engineering www.plantengineering.com
- Types of Flexible Couplings: Various types of flexible couplings can be used, such as rubber element couplings, gear couplings, or diaphragm couplings, each with different misalignment capabilities.
4. Self-Adjustment (Limited):
- Oil Film Dynamics: Under ideal operating conditions, the hydrodynamic oil film can help to self-center the shaft within the bearing, compensating for minor misalignment.
- Bearing Wear: However, excessive or prolonged misalignment can lead to uneven wear on the bearing surface, which might eventually compromise its ability to self-adjust.
Limitations and Considerations:
- Limited Misalignment Tolerance: While plain bearings can handle some misalignment, their tolerance is limited compared to other bearing types. Excessive or persistent misalignment can lead to increased friction, wear, overheating, and potential bearing failure.
- Regular Alignment Checks: It’s important to regularly check and adjust the shaft alignment, especially after significant changes in the vessel’s loading condition, maintenance work on the propulsion system, or if any signs of bearing distress are observed.
In Summary:
Plain bearings, despite their inherent limitations in misalignment tolerance, can accommodate some degree of shaft misalignment through their design clearance, the hydrodynamic oil film, and the use of flexible couplings. However, regular alignment checks and maintenance are essential to ensure the system stays within acceptable limits and to prevent excessive wear or damage to the bearings.
Remember: If misalignment is suspected or if any signs of bearing distress (e.g., high temperature, unusual noise, vibration) are observed, prompt action should be taken to investigate and correct the alignment to prevent further damage and ensure the safe and efficient operation of the propulsion system.
Why the shaft must be able to move longitudinally
In propulsion shaft systems, intermediate shaft bearings of the plain bearing type require the shaft to have some degree of longitudinal movement (axial movement along its length) due to several key factors:
- Thermal Expansion:
- Temperature Changes: The shaft and other components in the propulsion system experience temperature changes during operation. This can be due to the heat generated by friction in the bearings, changes in ambient temperature, or variations in the temperature of the fluid being pumped (if the shaft passes through a pump or other equipment).
- Expansion and Contraction: As the temperature rises, the shaft expands, and as it cools, it contracts. This thermal expansion and contraction can cause significant changes in the shaft’s length.
- Accommodation: The bearings need to allow for this longitudinal movement to prevent excessive axial forces and stresses that could damage the bearings, seals, or other components in the system.
- Shaft Deflection:
- Operational Loads: The propeller shaft experiences various loads and forces during operation, including thrust from the propeller, torque from the engine, and bending moments due to the vessel’s motion in waves.
- Shaft Bending: These loads can cause the shaft to deflect or bend slightly along its length.
- Bearing Accommodation: The intermediate shaft bearings need to be able to accommodate this deflection without binding or creating excessive friction, which could lead to overheating and premature wear.
- Alignment Adjustments:
- Initial Alignment: During installation, the shafting system is aligned as precisely as possible. However, perfect alignment is challenging to achieve and maintain over time.
- Operational Changes: Changes in the vessel’s loading condition, wear and tear on components, or even minor impacts can cause slight misalignments.
- Adjustment Flexibility: The ability of the shaft to move longitudinally allows for minor adjustments in alignment during maintenance or repairs, ensuring proper load distribution on the bearings and preventing excessive wear.
- Assembly and Disassembly:
- Maintenance and Repairs: During maintenance or repairs, it’s often necessary to remove or replace components within the shafting system.
- Ease of Access: Allowing for longitudinal movement of the shaft facilitates the removal and installation of couplings, bearings, and other components, making maintenance tasks easier and more efficient.
How Longitudinal Movement is Allowed
- Bearing Design: Plain bearings are typically designed with a clearance between the shaft journal and the bearing surface, allowing for some axial movement.
- Thrust Bearings: Dedicated thrust bearings are installed at specific points in the shafting system to handle the axial thrust generated by the propeller and control the shaft’s longitudinal position.
- Flexible Couplings: Flexible couplings, installed between shaft sections, can also accommodate some degree of axial movement, further enhancing the system’s ability to handle changes in shaft length and alignment.
In summary, the ability of the shaft to move longitudinally in a system with plain intermediate shaft bearings is crucial to accommodate thermal expansion, shaft deflection, alignment adjustments, and maintenance requirements. This flexibility helps to prevent excessive stresses, minimize wear and tear, and ensure the reliable and efficient operation of the propulsion system.
Why the aftmost bearing requires a complete bush
In propulsion shaft intermediate bearings of the plain bearing type, the aftmost bearing often requires a complete bush (a full cylindrical sleeve lining the bearing housing) while other bearings may only have a bush in the lower half. This design difference is attributed to the specific loads and functions of these bearings.
Aftmost Bearing:
- Supports Shaft Weight: The aftmost bearing, being the closest to the propeller, typically carries a significant portion of the propeller shaft’s weight.
- Absorbs Propeller Thrust: It also experiences some degree of thrust load from the propeller, especially during maneuvering or in rough seas.
- Complete Bush for Full Support: A complete bush provides 360-degree support to the shaft, ensuring adequate load-carrying capacity and stability, particularly under varying operating conditions and potential misalignment.
Other Intermediate Bearings:
- Reduced Load: Intermediate bearings located further forward on the shaft generally experience lower loads compared to the aftmost bearing. They primarily serve to guide and support the shaft, with less emphasis on carrying significant weight or thrust.
- Lower Half Bush: A bush in the lower half of the bearing is often sufficient to provide adequate support and lubrication under normal operating conditions.
- Upper Half Clearance: The upper half of the bearing may have a larger clearance or even no bush at all, allowing for some degree of shaft deflection and thermal expansion without causing excessive friction or binding.
- Oil Film Support: The hydrodynamic oil film generated during operation helps to further support the shaft in the upper half, even with a larger clearance.
Benefits of this Design Approach:
- Cost-Effectiveness: Using a partial bush in some bearings reduces material costs and complexity compared to using full bushes in all bearings.
- Reduced Friction: The larger clearance in the upper half of some bearings can reduce friction and heat generation under normal operating conditions.
- Accommodation of Misalignment: The combination of bearing clearance and flexible couplings allows for some degree of shaft misalignment, enhancing the system’s adaptability to varying loads and operating conditions.
Important Considerations:
- Bearing Load Analysis: The specific bearing design and whether a full or partial bush is used depends on careful analysis of the expected loads and operating conditions for each bearing location.
- Maintenance and Inspection: Regular inspection and maintenance are crucial to ensure the bearings are in good condition and the clearances are within acceptable limits. Excessive wear or misalignment can lead to increased friction, overheating, and potential bearing failure.
In summary, the aftmost bearing in a propulsion shaft system often requires a complete bush due to the higher loads it experiences, while other intermediate bearings might use a partial bush in the lower half to provide adequate support while allowing for some flexibility and reduced friction. This design approach balances the need for load-carrying capacity and alignment tolerance with cost-effectiveness and efficiency considerations.