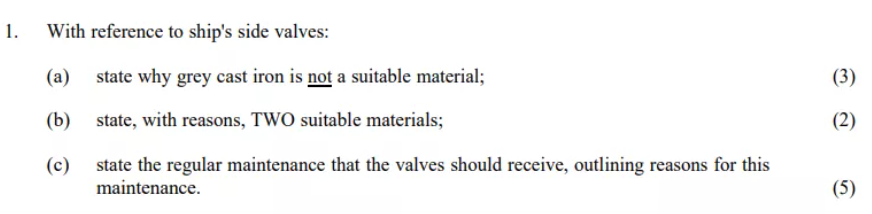
With reference to ship’s side valves:
(a) state why grey cast iron is not a suitable material;(3)
(b) state, with reasons, TWO suitable materials;(2)
(c) state the regular maintenance that the valves should receive, outlining reasons for this maintenance.(5)
Question 1. The question specifically refers to ship side valves, many give answers based on general properties of cast iron in sea water.
Ship’s side valves
Ship’s side valves, also referred to as sea valves or hull valves, are crucial components installed on the hull of a vessel, including superyachts. These valves control the flow of seawater into and out of the vessel for various systems.
1. Flooding risk to machinery spaces of floating offshore installations: Guidelines on inspection of ship side valves – HSE
Key Purposes:
- Seawater Intake: Ship’s side valves allow seawater to be drawn into the vessel for various purposes, such as:
- Engine Cooling: Providing a continuous supply of seawater to cool the main engines and generators.
- Air Conditioning: Supplying seawater to chillers for air conditioning systems.
- Firefighting: Feeding the fire main system with seawater for firefighting purposes.
- Other Systems: Supplying seawater to other systems that require it, such as certain sanitation systems or deck wash systems.
- Discharges: Ship’s side valves also control the discharge of various fluids from the vessel into the sea, such as:
- Engine Cooling Water Discharge: Releasing the heated seawater used for engine cooling back into the sea.
- Bilge Water Discharge: Discharging bilge water, which is a mixture of water, oil, and other fluids collected in the bilges of the vessel.
- Sewage Discharge: Releasing treated or untreated sewage from the vessel’s sanitation system.
- Other Discharges: Discharging other fluids as needed, such as greywater from sinks and showers or certain industrial wastewater.
Key Features:
- Located on the Hull: Ship’s side valves are directly connected to the hull of the vessel, penetrating through the shell plating.
- Robust Construction: They are built to withstand the harsh marine environment and the pressures associated with seawater intake and discharge.
- Various Types: Different types of valves are used depending on the application, such as gate valves, ball valves, butterfly valves, and non-return valves.
- Manual or Remote Operation: They can be operated manually or remotely, depending on their location and function.
Importance:
- Essential for Operation: Ship’s side valves are critical for the operation of various onboard systems that rely on seawater intake or discharge.
- Safety and Environmental Protection: They must be properly maintained and operated to prevent flooding, pollution, and other hazards.
- Regulatory Compliance: The design, installation, and operation of ship’s side valves are subject to strict regulations to ensure safety and environmental protection.
In essence, ship’s side valves act as the gateways between the vessel’s internal systems and the surrounding marine environment. They enable crucial functions while also posing potential risks if not properly managed. Understanding their operation, maintenance, and associated regulations is vital for anyone involved in the operation or maintenance of a superyacht or any seagoing vessel.
Grey cast iron
Grey cast iron, despite its strength and affordability, is generally not considered a suitable material for ship’s side valves on superyachts (or most seagoing vessels) for several key reasons:
- Corrosion Susceptibility: Grey cast iron is prone to corrosion in marine environments due to its high carbon content and exposure to saltwater. Corrosion can weaken the valve body and lead to leaks, potentially causing flooding and compromising the vessel’s safety.
- Brittleness: Grey cast iron is relatively brittle compared to other materials like bronze or stainless steel. It can be susceptible to cracking or fracturing under stress, especially in dynamic marine environments with vibrations, impacts, and temperature fluctuations. 1. Stainless Steel vs Cast Iron: A Detailed Comparison – Tuolian tuolianmetal.com2. Fracture morphology and fracture mechanism of gray cast iron with scrap – ZHY Casting www.zhycasting.com
- Difficulty in Repair: Once a grey cast iron valve corrodes or cracks, it is challenging to repair effectively. Welding or patching can be difficult and may not provide a reliable long-term solution.
- Environmental Concerns: In case of a leak or failure, grey cast iron can release iron oxide (rust) into the surrounding seawater, contributing to marine pollution.
- Regulatory Restrictions: Many classification societies and maritime regulations discourage or even prohibit the use of grey cast iron for ship’s side valves due to its inherent limitations and potential safety and environmental risks.
Preferred Materials:
- Bronze: A copper alloy known for its excellent corrosion resistance in marine environments. It also offers good strength and machinability, making it suitable for ship’s side valves. 1. A Guide to Different Types of Bronze Alloys – MetalTek International www.metaltek.com
- Stainless Steel: Another excellent choice for its superior corrosion resistance and strength. While more expensive, it provides long-term durability and reduced maintenance requirements.
In summary: Grey cast iron’s susceptibility to corrosion, brittleness, and difficulty in repair make it unsuitable for the demanding conditions of ship’s side valves. Materials like bronze or stainless steel, with their superior corrosion resistance and durability, are preferred to ensure the safety, reliability, and longevity of these critical components.
Suitable materials for ship’s side valves
Suitable materials for ship’s side valves need to be robust and highly resistant to corrosion due to constant exposure to seawater. Here are some commonly used materials and their benefits:
1. Different Types Of Ship Valves For Industrial Use – DomBor Valve
- Bronze:
- Excellent Corrosion Resistance: Bronze alloys, particularly those containing aluminum or silicon, form a protective oxide layer that resists corrosion in seawater. 1. Aluminium bronze – a corrosion resistant metal in sea water – AMPCO Academy academy.ampcometal.com
- Strength and Durability: Bronze is strong and durable, capable of withstanding the pressures and stresses associated with ship’s side valve applications. 1. Why Cast Bronze Is Stronger Than Most Alloys – Wieland Diversified Metals www.wieland-diversified.com
- Good Machinability: It’s relatively easy to machine and cast into complex shapes required for valves.
- Stainless Steel:
- Superior Corrosion Resistance: Stainless steels, particularly those with high chromium and molybdenum content (like 316 stainless steel), offer exceptional corrosion resistance in marine environments. 1. Corrosion Resistance in Marine Environments www.assda.asn.au
- High Strength: They are strong and durable, suitable for high-pressure applications. 1. Stainless steel – Wikipedia en.wikipedia.org
- Hygiene: Stainless steel surfaces are easy to clean and maintain, important for systems like potable water or food handling. 1. Stainless steel is easy to keep clean – Outokumpu www.outokumpu.com
- Copper-Nickel Alloys:
- Excellent Corrosion Resistance: These alloys, often referred to as “naval brass” or “cupronickel,” exhibit superior resistance to seawater corrosion and biofouling (the accumulation of marine organisms). 1. Cu-Ni Alloy Resistance to Corrosion and Biofouling – Copper Development Association www.copper.org
- Good Strength and Ductility: They offer a good balance of strength and ductility, making them suitable for various ship’s side valve applications.
- Duplex Stainless Steels:
- High Strength and Corrosion Resistance: These steels combine the properties of austenitic and ferritic stainless steels, offering exceptional strength and corrosion resistance, especially in harsh marine environments. 1. Duplex Stainless Steel: The Superior Choice for Marine and Corrosive Environments spenglerindustries.com
- Cost-Effective: While more expensive than standard stainless steels, their superior properties can lead to long-term cost savings due to reduced maintenance and replacement needs. 1. Duplex Stainless Steel: Advantages and Applications – Sree Metaliks sreemetaliks.com
Why These Materials are Suitable:
- Corrosion Resistance: The primary concern for ship’s side valves is corrosion due to constant exposure to seawater. The materials listed above have proven track records of resisting corrosion and ensuring the longevity of the valve.
- Strength and Durability: Ship’s side valves must be able to withstand significant pressures and stresses from both internal system pressures and external forces like wave impacts. These materials offer the necessary strength and durability for such demanding applications.
- Biofouling Resistance: Some materials, like copper-nickel alloys, inherently resist the attachment and growth of marine organisms, which can impair valve function and lead to maintenance issues. 1. Cu-Ni Alloy Resistance to Corrosion and Biofouling – Copper Development Association www.copper.org
- Ease of Maintenance: These materials are generally easy to machine, weld, and maintain, facilitating repairs and replacements when necessary.
The specific material choice for a ship’s side valve will depend on various factors, including the system it serves, the operating conditions, budget considerations, and any specific regulatory requirements. However, prioritizing corrosion resistance, strength, and durability is crucial for ensuring the safety and reliability of ship’s side valves in the harsh marine environment.
Regular maintenance of valves
Regular maintenance of valves, particularly in critical systems like a superyacht’s fire main, is vital to ensure their proper function and reliability when needed. Here’s the recommended maintenance schedule along with the reasons behind each task:
1. Visual Inspection
- Frequency: Monthly or more frequently in harsh environments.
- Purpose:
- Check for signs of corrosion, leaks, or physical damage to the valve body, bonnet, stem, or handwheel.
- Identify any loose or missing components, such as bolts, nuts, or nameplates.
- Look for any signs of external damage or wear on the valve’s protective coatings.
- Verify that the valve is properly labeled and accessible.
2. Operational Test
- Frequency: Quarterly or more frequently for critical valves.
- Purpose:
- Ensure the valve operates smoothly and fully opens and closes without any binding or sticking.
- Check for any unusual noises or vibrations during operation.
- Verify that the valve provides a tight seal when closed.
3. Lubrication
- Frequency: Annually or as recommended by the manufacturer.
- Purpose:
- Apply lubricant to moving parts like the stem and packing gland to reduce friction and wear, ensuring smooth operation.
- Prevent the stem from seizing or becoming difficult to operate.
4. Packing Adjustment/Replacement
- Frequency: Annually or as needed based on inspection and leakage.
- Purpose:
- Check the packing gland for leaks and adjust it if necessary to maintain a tight seal around the stem.
- Replace the packing material if it’s worn, damaged, or causing excessive leakage.
5. Internal Inspection and Cleaning
- Frequency: Annually or as recommended by the manufacturer, or if the valve is suspected of being contaminated or malfunctioning.
- Purpose:
- Disassemble the valve to inspect internal components like the seat, disc, and stem for wear, corrosion, or damage.
- Clean any debris or buildup that may be affecting valve performance.
- Replace worn or damaged internal components as needed.
6. Functional Testing
- Frequency: Varies depending on the system and criticality of the valve, but typically at least annually or after any maintenance or repair.
- Purpose:
- Conduct specific tests to verify the valve’s performance under operating conditions. This might include pressure testing to confirm its ability to hold pressure, or flow testing to assess flow rates and identify any restrictions.
Reasons for Regular Maintenance:
- Ensure Operational Readiness: Regular maintenance ensures that valves are in good working condition and will operate reliably when needed, especially in critical situations like a fire.
- Prevent Corrosion and Wear: Marine environments are harsh, and corrosion and wear can degrade valves over time. Maintenance helps identify and address these issues before they lead to failure.
- Extend Valve Lifespan: Proper maintenance can significantly extend the lifespan of valves, reducing the need for costly replacements.
- Comply with Regulations: Classification societies and maritime regulations often require periodic maintenance and testing of safety-critical equipment like fire main valves.
By adhering to a regular maintenance schedule and addressing any issues promptly, ship owners and operators can ensure the continued reliability and effectiveness of their valves, contributing to the overall safety and operational efficiency of the vessel.