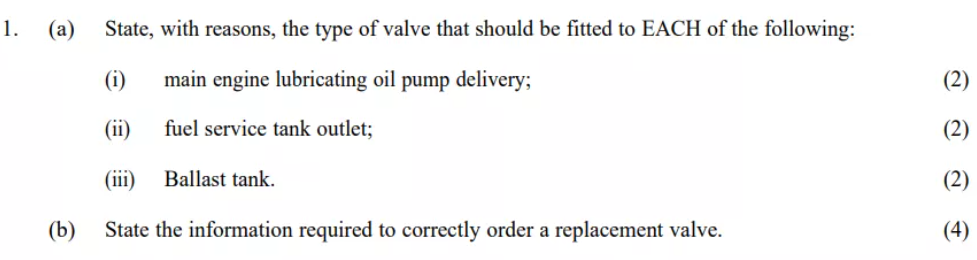
(a) State, with reasons, the type of valve that should be fitted to EACH of the following:
(i) main engine lubricating oil pump delivery;(2)
(ii) fuel service tank outlet;(2)
(iii) Ballast tank.(2)
(b) State the information required to correctly order a replacement valve.(4)
Globe Valve
For a main engine lubricating oil pump delivery, a Globe Valve would be the most suitable choice. Here’s why:
- Throttling Capability: Globe valves excel at regulating flow. This is crucial in a lubricating oil system as oil flow needs to be precisely controlled to maintain optimal engine lubrication and avoid damage.
- Good Shut-off: Globe valves provide a tight seal when fully closed, preventing any leakage of oil when the system is not in use or during maintenance.
- Durability: Globe valves are generally robust and durable, able to handle the pressures and temperatures typically found in lubricating oil systems.
- Directional Flow: The design of globe valves inherently handles unidirectional flow, which is the typical requirement for a pump delivery line.
While other valve types like ball valves or butterfly valves might offer advantages in some applications, their suitability for this specific scenario is limited:
- Ball Valves: While excellent for on/off control, they are not as effective at fine flow regulation, which is necessary for lubricating oil systems.
- Butterfly Valves: They can handle large flow rates but might not provide the same level of tight shut-off as a globe valve, potentially leading to oil leaks when the system is not in use.
In summary, a globe valve’s ability to precisely control flow, its tight shut-off capability, and its overall durability make it the best fit for regulating the delivery of lubricating oil from the main engine pump.
Ball Valve
For a fuel service tank outlet, the most suitable valve type is a Ball Valve. Here’s why:
- Excellent Shut-off: Ball valves are renowned for their ability to provide a tight, reliable seal when closed. This is critical for fuel systems, as any leakage could lead to fire hazards or environmental pollution. 1. Ball Valves vs Gate Valves INOX-TEK OEM Valves Manufacturer www.inox-tek.com.tw
- Quick Operation: They are quick and easy to operate, typically requiring only a quarter-turn of the handle to go from fully open to fully closed. This is advantageous in emergency situations where rapid fuel shut-off may be necessary. 1. Everything You Need to Know About Ball Valves redwhitevalvecorp.com
- Minimal Flow Restriction: When fully open, ball valves offer a full bore flow path, meaning there’s minimal restriction to the flow of fuel. This ensures efficient fuel delivery to the engine or other systems. 1. Everything You Need to Know About Ball Valves redwhitevalvecorp.com
- Durability: Ball valves are generally durable and can withstand the pressures and temperatures encountered in fuel systems. They are also less prone to wear and tear compared to some other valve types. 1. Gate Valves vs. Ball Valves: How to Choose the Right One – Gemini Valve www.geminivalve.com2. Ball Valves vs. Globe Valves qrcvalves.com
- Low Maintenance: They typically require minimal maintenance, which is beneficial in marine environments where access to components can be limited.
While other valve types like gate valves or butterfly valves could technically be used, they have certain limitations compared to ball valves for this specific application:
- Gate Valves: Although they offer excellent shut-off and full bore flow, gate valves are slower to operate and may not be ideal for quick shut-off in emergencies. 1. Gate Valve Disadvantages: What You Need to Know www.everlastingvalveusa.com
- Butterfly Valves: While compact and relatively easy to operate, butterfly valves may not provide the same level of tight sealing as ball valves, especially over time with wear and tear.
Overall, ball valves offer the best combination of tight shut-off, quick operation, minimal flow restriction, durability, and low maintenance, making them the preferred choice for fuel service tank outlet valves.
Ballast Tank
For a ballast tank, the most suitable type of valve is typically a Butterfly Valve or a Gate Valve, depending on specific requirements and location.
Butterfly Valve:
- Advantages:
- Quick Operation: Butterfly valves can be opened and closed quickly with a simple quarter-turn operation, which is important for efficient ballast operations.
- Compact Design: They have a compact design, making them ideal for installations where space is limited.
- Lightweight: Butterfly valves are generally lighter than gate valves, reducing the overall weight and complexity of the ballast system.
- Good for Throttling: While not as precise as globe valves, butterfly valves can be used to some extent for throttling flow, providing additional control over ballasting and de-ballasting operations.
- Disadvantages:
- Less Tight Shut-Off: Compared to gate valves, butterfly valves might not provide as tight a seal, especially over time with wear and tear. This could lead to minor leakage in some cases.
- Higher Pressure Drop: The disc in a butterfly valve obstructs the flow path even when fully open, resulting in a slightly higher pressure drop compared to gate valves.
Gate Valve:
- Advantages:
- Excellent Shut-off: Gate valves provide a very tight seal when closed, ensuring minimal to no leakage from the ballast tank. This is important to prevent unintended changes in the ship’s trim and stability.
- Full Bore Design: They offer a full bore design, meaning the internal diameter of the valve matches the pipe diameter, minimizing flow restriction and pressure drop.
- Durability: Gate valves are robust and can withstand the harsh marine environment and the pressures associated with ballast systems.
- Disadvantages:
- Slower Operation: Gate valves require multiple turns of the handwheel or actuator to open or close, which can be slower compared to butterfly valves.
- Bulkier Design: They tend to be bulkier and heavier than butterfly valves, potentially adding to the complexity and weight of the ballast system.
Choosing Between Butterfly and Gate Valves:
- Location:
- Remotely Operated Valves: For ballast tanks located in inaccessible areas or where remote operation is required, butterfly valves are often preferred due to their quick operation and compact design.
- Manually Operated Valves: For tanks with readily accessible valves, gate valves might be a suitable choice due to their superior shut-off capabilities.
- System Requirements:
- Tight Shut-off Critical: If a very tight seal is crucial to prevent any leakage from the ballast tanks, gate valves would be the preferred option.
- Quick Operation Needed: If rapid ballasting and de-ballasting operations are important, butterfly valves might be more suitable.
Ultimately, the choice between butterfly and gate valves for ballast tanks depends on a balance between operational requirements, space constraints, budget, and the level of shut-off required. Both types of valves are commonly used in ballast systems and, when properly selected and maintained, can provide reliable and effective control of ballast water.
Replacement valve information
To correctly order a replacement valve, the following information is typically required:
- Valve Type: Specify the exact type of valve needed (e.g., gate valve, ball valve, globe valve, butterfly valve, etc.). This ensures you get the right valve for the intended application.
- Size: Provide the size of the valve, typically expressed as the nominal pipe size (NPS) or diameter in inches or millimeters. This ensures the valve will fit properly in the existing piping system.
- Material: Specify the material of the valve body and other critical components. Common materials include bronze, brass, cast iron, stainless steel, etc. The material choice is important for compatibility with the fluid being handled, pressure and temperature ratings, and corrosion resistance.
- Pressure Rating: Indicate the maximum pressure the valve needs to withstand. This is usually expressed in pounds per square inch (psi) or bar.
- Temperature Rating: Specify the maximum and minimum temperatures the valve will be exposed to. This ensures the valve can handle the operating conditions without damage or failure.
- Connection Type: Indicate the type of connection the valve needs to have to fit into the existing piping system. Common connection types include flanged, threaded, socket-weld, or butt-weld.
- Flow Direction: If applicable, specify the intended flow direction through the valve, especially for valves designed for unidirectional flow (e.g., check valves or some globe valves).
- Actuation Type: If the valve is not manually operated, specify the type of actuation required (e.g., pneumatic, hydraulic, electric). Also, provide details about the actuator’s specifications, such as voltage, pressure, or torque requirements.
- Trim Material: Specify the material of the internal trim components, such as the seat, disc, or stem. This is important for compatibility with the fluid being handled and to ensure proper sealing and wear resistance.
- Manufacturer and Model Number: If you are replacing an existing valve, providing the manufacturer and model number can simplify the ordering process and ensure you get an exact match.
- Any Special Requirements: If the valve needs to meet any specific certifications, standards, or have additional features (e.g., a bypass valve, drain valve, or position indicator), be sure to specify those as well.
- Quantity: Indicate the number of valves required.
By providing this comprehensive information, you can help ensure you receive the correct replacement valve that meets the specific needs of your application and integrates seamlessly into your system.