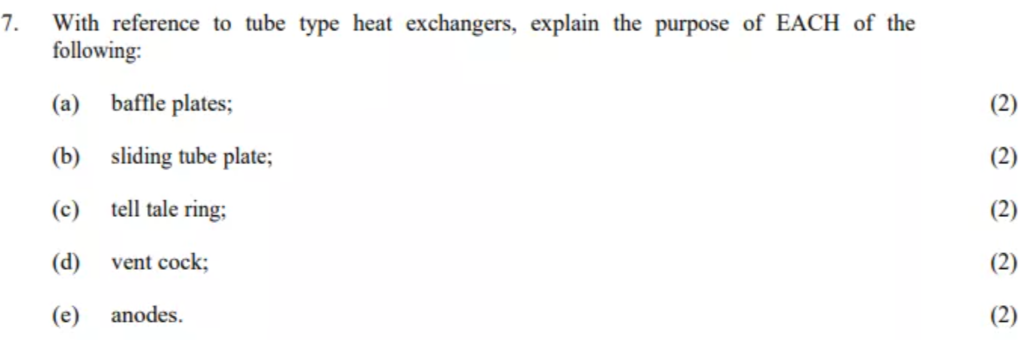
With reference to tube type heat exchangers, explain the purpose of EACH of the following:
(a) baffle plates;(2)
(b) sliding tube plate;(2)
(c) tell tale ring;(2)
(d) vent cock;(2)
(e) anodes.(2)
Tube Type Heat Exchangers
A tube type heat exchanger, often referred to as a shell and tube heat exchanger, is a device used to transfer heat between two fluids. It consists of a bundle of tubes enclosed within a cylindrical shell.
1. Shell and Tube Heat Exchanger: Understanding its Function and Operation – Alaqua Inc
2. Shell and Tube or Plate Type? – Thermex Heat Exchangers
How it works:
- Fluid flow: One fluid flows through the tubes, while the other fluid circulates around the tubes within the shell. 1. Vertical Shell And Tube Fluidized Bed Heat Exchanger Fouling – Klaren International Bv klarenbv.com
- Heat transfer: Heat is exchanged between the two fluids through the tube walls. 1. Double Tube Heat Exchanger: Design & Double Wall Structure – StudySmarter www.studysmarter.co.uk
- Efficiency: The large surface area of the tubes allows for efficient heat transfer. 1. Advantages Of Using Heat Exchanger Tube Thickness In Construction And Infrastructure Projects www.mbmtubes.com
Components:
- Shell: The cylindrical housing that contains the tube bundle. 1. Shell-and-tube heat exchanger – Wikipedia en.wikipedia.org
- Tubes: The tubes through which one fluid flows. 1. Shell-and-tube heat exchanger – Wikipedia en.wikipedia.org
- Tube sheets: Support the tubes at each end of the shell. 1. Shell and Tube Heat Exchanger: What Is It? Types, Process – IQS Directory www.iqsdirectory.com
- Baffles: Used to direct the flow of the shell-side fluid for improved heat transfer. 1. Shell and Tube Heat Exchanger: What Is It? Types, Process – IQS Directory www.iqsdirectory.com
- Nozzles: Inlet and outlet connections for both fluids. 1. 2.3. Parts of typical shell and tube heat exchanger. A – ResearchGate www.researchgate.net
Types of Tube Arrangements:
U-tube: Tubes are bent into a U-shape, allowing for thermal expansion without requiring expansion joints. 1. Types of Shell and Tube Heat Exchanger | Sterling TT www.sterlingtt.com
Fixed tube sheet: Tubes are fixed to the tube sheets, limiting thermal expansion. 1. Fixed Tube | Heat Exchangers www.shell-tube.com
Floating head: One tube sheet is fixed, while the other is allowed to move to accommodate thermal expansion. 1. Heat Exchanger Differential Thermal Expansion – CMS Heat Transfer Division, Inc. www.cmsheattransfer.com
Tube type heat exchangers are widely used in various industries due to their versatility, efficiency, and reliability.
1. Is a Shell & Tube Heat Exchanger Right for You? – Boilersource
Baffle Plates in Tube Type Heat Exchangers
Many tube type heat exchangers incorporate baffle plates.
1. SHELL AND TUBE HEAT EXCHANGERS – Thermopedia
Purpose of Baffle Plates:
- Improved Heat Transfer: By creating turbulence in the shell-side fluid, baffle plates increase the fluid velocity and enhance heat transfer between the two fluids. 1. What’s the Heat Exchanger Baffle Plate? www.jetvisionengineering.com
- Support for Tubes: Baffle plates can also provide structural support for the tube bundle. 1. Baffle plate Persentation | PPT – SlideShare www.slideshare.net
- Fluid Distribution: They help distribute the shell-side fluid evenly across the tube bundle.
Types of Baffle Plates:
- Segmental Baffles: These are the most common type, with curved plates dividing the shell into segments.
- Disc and Doughnut Baffles: These consist of a central disk surrounded by a ring, creating annular flow passages.
- Plate and Frame Baffles: Used in plate and frame heat exchangers, these plates create a series of flow channels. 1. Plate and Frame Heat Exchanger – How It Works | RasMech www.rasmech.com
The type of baffle plate used depends on factors such as the desired heat transfer rate, pressure drop, and the fluids involved.
Opens in a new windowtungaloy.com
tube type heat exchanger with baffle plates
Sliding Tube Plate Heat Exchanger
A sliding tube plate heat exchanger is a type of shell and tube heat exchanger designed to accommodate thermal expansion and contraction.
How it works:
- Floating Tube Sheet: One of the tube sheets is allowed to move axially within the shell to compensate for thermal expansion. 1. Heat Exchanger Differential Thermal Expansion – CMS Heat Transfer Division, Inc. www.cmsheattransfer.com
- Gaskets: Seals are used between the sliding tube sheet and the shell to prevent leakage.
- Guides: The sliding tube sheet is often guided by rods or rails to ensure smooth movement.
Advantages:
- Accommodates thermal expansion: Prevents tube damage due to thermal stresses.
- Reduced maintenance: Less prone to leaks compared to fixed tube sheet designs.
Disadvantages:
- More complex design: Requires additional components and seals.
- Potential for leakage: If not properly maintained, gaskets can fail, leading to leakage.
While sliding tube plate heat exchangers offer advantages in terms of thermal expansion, they require careful design and maintenance to ensure optimal performance and reliability.
Opens in a new windowhassanelbanhawi.com
sliding tube plate heat exchanger
Tell-Tale Ring in Marine Heat Exchangers
A tell-tale ring is a diagnostic feature in some types of heat exchangers, particularly shell-and-tube heat exchangers.
Purpose:
- Leak detection: It indicates leakage between the two fluids being exchanged (e.g., seawater and lubricating oil).
- Early warning: Allows for timely maintenance or repair before the leak becomes more severe.
How it works:
- Placement: The tell-tale ring is typically located at the joint between the tube bundle and the water box.
- Leakage: If there’s a leak in the joint, the leaking fluid will accumulate in the tell-tale ring area.
- Visual inspection: By periodically checking the tell-tale ring for fluid accumulation, maintenance personnel can detect leaks early.
Importance:
Early detection of leaks in heat exchangers is crucial to prevent equipment damage, contamination of fluids, and potential environmental hazards. The tell-tale ring is a simple but effective tool for achieving this.
Purpose of Vent Cocks in Tube Type Heat Exchangers
Vent cocks are fitted to tube type heat exchangers to facilitate the removal of air pockets during filling and operation.
Reasons for using vent cocks:
- Air Removal: When a heat exchanger is initially filled, air pockets can form, reducing its efficiency. Vent cocks allow this air to escape.
- Pressure Relief: In some cases, vent cocks can also act as a pressure relief device to prevent excessive pressure buildup.
- Maintenance: During maintenance or cleaning, vent cocks can be used to drain the heat exchanger completely.
Typically, vent cocks are located at the highest point of the heat exchanger.
By using vent cocks, it is possible to ensure that the heat exchanger is filled completely with fluid, improving its performance and preventing potential damage due to air pockets.
Anodes in Tube Type Heat Exchangers
Anodes are fitted to tube type heat exchangers in marine environments to protect the metal components from corrosion.
How they work:
- Sacrificial protection: Anodes are made of a metal that is more susceptible to corrosion than the materials used in the heat exchanger. 1. Sacrificial Anodes | American Galvanizers Association galvanizeit.org
- Electrochemical reaction: The anode corrodes preferentially, acting as a sacrificial metal to protect the heat exchanger. 1. Sacrificial Anodes – Condenser & Chiller Services www.ccs-tubes.com
- Corrosion prevention: By corroding instead of the heat exchanger, the anode extends the lifespan of the equipment.
Common anode materials:
- Zinc: Widely used due to its effectiveness and cost-efficiency.
- Aluminum: Offers higher corrosion protection but is more expensive.
Placement:
- Seawater side: Anodes are typically installed on the seawater side of the heat exchanger, as this is the most corrosive environment.
- Strategic locations: Anodes are positioned in areas prone to corrosion, such as the tube sheets and end covers.
By using anodes, the lifespan of the heat exchanger can be significantly extended, reducing maintenance costs and downtime.