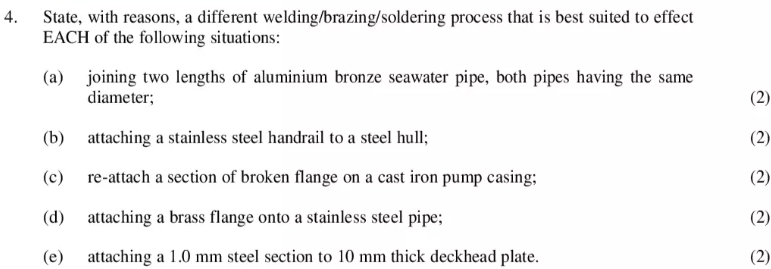
State, with reasons, a different welding/brazing/soldering process that is best suited to effect EACH of the following situations:
(a) joining two lengths of aluminium bronze seawater pipe, both pipes having the same diameter;(2)
(b) attaching a stainless steel handrail to a steel hull;(2)
(c) re-attach a section of broken flange on a cast iron pump casing;(2)
(d) attaching a brass flange onto a stainless steel pipe;(2)
(e) attaching a 1.0 mm steel section to 10 mm thick deckhead plate.(2)
Welding, Brazing, and Soldering in Marine Engineering
Marine engineering employs a variety of joining processes to construct, repair, and maintain vessels. Here are some of the most common:
1. List of Processes Used in Marine Workshop of Ships – Scribd
Welding Processes
- Shielded Metal Arc Welding (SMAW): Also known as stick welding, it uses a coated electrode to create an arc and weld metals. 1. Shielded Metal Arc Welding (SMAW): Definition, How It Works, and Advantages | Xometry www.xometry.com
- Gas Metal Arc Welding (GMAW): Commonly known as MIG welding, it uses a continuous wire electrode and shielding gas. 1. Gas Metal Arc Welding (GMAW) – Technoweld technoweld.com.au
- Gas Tungsten Arc Welding (GTAW): Also known as TIG welding, uses a non-consumable tungsten electrode and shielding gas. 1. Why choose GTAW (Gas Tungsten Arc Welding) ? – AXXAIR www.axxair.com
- Submerged Arc Welding (SAW): Uses a submerged arc and granular flux to create a weld. 1. Submerged Arc Welding Process – TWI Global www.twi-global.com
- Laser Beam Welding (LBW): A high-power laser beam melts the base materials to create a weld. 1. Laser Welding: Definition, How it Works, Process, Types, and Advantages | Xometry www.xometry.com
Brazing Processes
- Furnace Brazing: Heating the assembly in a furnace to melt the brazing filler metal. 1. Welding & Joining Technology: Brazing, Braze Welding, and Soldering. – LibGuides wiregrass.libguides.com
- Torch Brazing: Using a gas torch to heat the assembly and melt the brazing filler metal. 1. | Torch Brazing – Precision Metal Industries pmiquality.com
Soldering
- Soft Soldering: Joining metals using a low-melting point alloy, typically lead-based or tin-based.
Note: While soldering is used in some applications, welding and brazing are more common in marine engineering due to the higher strength requirements.
Other Processes
- Riveting: Although less common in modern shipbuilding, riveting is still used in some applications.
- Adhesive Bonding: Used for joining non-metallic or dissimilar materials. 1. The Different Types of Adhesive Bonding Materials I Strouse www.strouse.com
The choice of process depends on factors such as material type, thickness, joint design, and desired joint properties.
Joining Aluminum Bronze Seawater Pipes
For joining two lengths of aluminum bronze seawater pipe with the same diameter, the following processes are typically suitable:
Welding Processes:
- Gas Tungsten Arc Welding (TIG): Offers excellent control and weld quality, ideal for aluminum bronze.
- Plasma Arc Welding (PAW): Similar to TIG but with higher energy density, providing deeper penetration.
Other Processes:
- Brazing: Can be used for joining thinner pipes, but the strength of the joint might be lower than welding.
Important considerations:
- Material Compatibility: Ensure the filler metal or brazing alloy is compatible with aluminum bronze.
- Surface Preparation: Proper cleaning and preparation of the pipe ends are crucial for a strong joint.
- Corrosion Prevention: Implement measures to prevent galvanic corrosion if joining to other metals.
- Post-Weld Heat Treatment: Some welding processes might require post-weld heat treatment to improve the joint properties.
Note: While other welding processes like MIG and SAW can be used, TIG and PAW are generally preferred for aluminum bronze due to their control and ability to prevent contamination.
Joining a Stainless Steel Handrail to a Steel Hull
For attaching a stainless steel handrail to a steel hull, welding is typically the most suitable method. Specifically, these processes are commonly used:
- Gas Metal Arc Welding (MIG): Offers good speed and weld quality for this application.
- Shielded Metal Arc Welding (SMAW): More versatile but generally slower than MIG.
- Tungsten Inert Gas (TIG) Welding: Provides excellent control and weld quality but is slower than MIG.
Key considerations:
- Material Compatibility: Ensure the welding process and filler metal are compatible with both stainless steel and mild steel.
- Galvanic Corrosion: While less severe than joining aluminum to steel, consider potential galvanic corrosion and implement protective measures if necessary.
- Weld Quality: The weld must be strong, durable, and resistant to corrosion.
- Appearance: The weld should be aesthetically pleasing, especially in visible areas.
Other methods, such as bolting or adhesive bonding, might be considered for specific applications or in conjunction with welding.
Reattaching a Broken Cast Iron Flange to a Pump Casing
Reattaching a broken cast iron flange to a pump casing is a challenging task due to the brittle nature of cast iron and the critical nature of the component. Here are some potential methods:
Welding:
- Challenges: Cast iron is difficult to weld due to its tendency to crack. Preheating and post-weld heat treatment are often required. 1. Guidelines for Welding Cast Iron – Lincoln Electric www.lincolnelectric.com
- Process: If welding is attempted, consider using a low-hydrogen electrode and preheating the component to reduce the risk of cracking. Post-weld heat treatment might be necessary to relieve stresses.
Brazing:
- Advantages: Offers lower heat input compared to welding, reducing the risk of cracking. 1. Metal Joining: Brazing vs Welding – Lucas Milhaupt www.lucasmilhaupt.com
- Process: Requires careful cleaning of the surfaces, use of a suitable brazing alloy, and controlled heating.
Mechanical Fasteners:
- Studs and Nuts: Drilling and tapping holes in both the flange and casing to insert studs and nuts can provide a mechanical connection.
- Clamps: Depending on the geometry, clamps can be used to secure the flange to the casing.
Composite Repair:
- Epoxy-based materials: Using a high-strength epoxy to bond the broken flange back to the casing.
- Reinforcement: Additional reinforcement, such as metal or fiberglass mesh, can be incorporated for added strength.
Replacement:
- If the damage is extensive or the repair is deemed unreliable, replacing the entire flange might be the best option.
Important Considerations:
- Stress Analysis: Conduct a stress analysis to determine the load on the flange and select the repair method accordingly.
- Material Compatibility: Ensure the materials used for repair are compatible with cast iron and the operating environment.
- Leak Testing: Thoroughly test the repaired component for leaks after completion.
It’s crucial to consult with a welding or repair specialist to determine the most suitable method for your specific situation.
Joining Brass Flange to Stainless Steel Pipe
Brazing is the most suitable method for joining a brass flange to a stainless steel pipe. This process involves melting a filler metal with a lower melting point than the base metals to create a joint.
1. Metal Joining: Brazing vs Welding – Lucas Milhaupt
Brazing Process:
- Surface Preparation: Both the brass flange and stainless steel pipe must be thoroughly cleaned and degreased.
- Flux Application: A flux is applied to the surfaces to prevent oxidation during the heating process. 1. Brazing Tutorial – Brass to Stainless Steel – YouTube m.youtube.com
- Heat Application: The joint is heated using a torch or induction heating until the brazing filler metal melts. 1. What is Brazing Metal: A Comprehensive Guide – DoDo Machine www.dodomachine.com
- Filler Metal Flow: The molten filler metal is drawn into the joint by capillary action, creating a strong bond. 1. Brazing Fundamentals – Lucas Milhaupt www.lucasmilhaupt.com
- Cooling: The assembly is allowed to cool slowly to ensure the integrity of the joint.
Key Considerations:
- Brazing Alloy: Choose a brazing alloy compatible with both brass and stainless steel.
- Surface Preparation: Proper cleaning is essential for optimal joint strength.
- Heating: Control the heating process to prevent overheating and damage to the materials.
- Filler Metal Application: Apply the filler metal evenly to ensure complete joint coverage.
- Cooling: Allow the joint to cool slowly to prevent cracking.
Brazing offers several advantages for this application, including:
- Strong and durable joint 1. Metal Joining: Brazing vs Welding – Lucas Milhaupt www.lucasmilhaupt.com
- Relatively easy to perform 1. Brazing Made Easy – YouTube m.youtube.com
- Less risk of damage to the base metals compared to welding 1. Brazing vs Welding: Understanding the Differences – Arccaptain www.arccaptain.com
Note: While welding can be used, it’s generally more complex and requires specialized equipment and expertise. Brazing is often preferred for this type of joint due to its simplicity and reliability.
Attaching a 1mm Steel Section to a 10mm Deckhead Plate
Given the significant difference in thickness between the 1mm steel section and the 10mm deckhead plate, welding would be the most suitable method for joining these components.
Welding Process:
- Gas Metal Arc Welding (MIG): Often the preferred choice due to its speed and ease of use.
- Gas Tungsten Arc Welding (TIG): Provides better control and weld quality but is slower.
- Shielded Metal Arc Welding (SMAW): Can be used but requires more skill and produces more slag.
Key Considerations:
- Joint Preparation: Ensure proper fit-up and beveling of the joint for optimal weld penetration.
- Welding Parameters: Carefully select welding parameters (voltage, amperage, wire feed speed) based on the materials and thicknesses involved.
- Preheating: For thicker deckhead plates, preheating might be necessary to prevent cracking.
- Post-Weld Heat Treatment: Depending on the specific materials and application, post-weld heat treatment might be required to improve weld properties.
Alternative Methods:
While welding is the most common method, other options could be considered depending on specific requirements:
Adhesive Bonding: Suitable for certain applications but generally not as strong as welding for this type of joint.
Bolting: Can be used for non-structural attachments but might not be suitable for load-bearing applications.