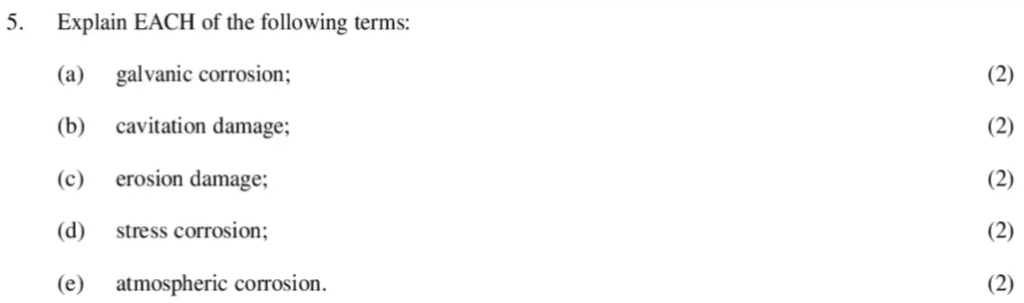
Explain EACH of the following terms:
(a) galvanic corrosion;(2)
(b) cavitation damage;(2)
(c) erosion damage;(2)
(d) stress corrosion;(2)
(e) atmospheric corrosion.(2)
Galvanic Corrosion
Galvanic corrosion occurs when two dissimilar metals are in electrical contact and immersed in an electrolyte (such as seawater). This creates a galvanic cell, where one metal acts as an anode and corrodes preferentially, while the other metal acts as a cathode and is protected.
The Process:
- Electrolyte: Seawater provides the conductive medium for ion movement.
- Electrode Formation: The more active metal becomes the anode, while the less active metal becomes the cathode. 1. Understanding Galvanic Corrosion: Concepts, Causes, and Prevention armoloy.com
- Ion Exchange: The anode metal releases ions into the electrolyte, creating an electric current. 1. Galvanic Corrosion & Galvanic Cell… – American Galvanizers Association galvanizeit.org
- Electron Flow: Electrons flow from the anode to the cathode through the metallic connection. 1. In a galvanic cell, the electrons flow from – BYJU’S byjus.com
- Corrosion: The anode metal corrodes as it loses electrons and ions, while the cathode is protected. 1. Galvanic Corrosion & Galvanic Cell… – American Galvanizers Association galvanizeit.org
Factors Affecting Galvanic Corrosion:Opens in a new windowbyjus.com galvanic corrosion
- Metal Potential Difference: The greater the difference in the electrochemical series between the two metals, the more severe the corrosion. 1. Why Do Two Dissimilar Metals Cause Corrosion? Exploring the Role of Galvanizing gaa.com.au
- Electrolyte Conductivity: Higher conductivity of the electrolyte (e.g., seawater with high salinity) increases corrosion rate.
- Metal Surface Area: A larger surface area of the anode relative to the cathode intensifies corrosion.
Preventing Galvanic Corrosion:
Coatings: Applying protective coatings to metal surfaces can act as a barrier. 1. Barrier Coating Benefits and Pitfalls – SilcoTek www.silcotek.com
Material Selection: Using similar metals or noble metals can reduce the risk. 1. Galvanic Corrosion: Avoidance and Risk Mitigation Explained – Unified Alloys www.unifiedalloys.com
Physical Separation: Isolating dissimilar metals can prevent electrical contact. 1. Galvanic Corrosion: Avoidance and Risk Mitigation Explained – Unified Alloys www.unifiedalloys.com
Sacrificial Anodes: Attaching a more reactive metal to act as a sacrificial anode. 1. Describe the function of a sacrificial anode. How is the function of a sacrificial anode similar to galvanization? – Vaia www.vaia.com
Impressed Current Cathodic Protection: Applying an external current to protect the structure. 1. Cathodic protection explained – Cathwell cathwell.com
Cavitation Damage
Cavitation is a phenomenon that occurs when a liquid is subjected to rapid changes in pressure, leading to the formation and collapse of vapor bubbles. This process can cause significant damage to solid surfaces.
1. What is Pump Cavitation and How to Prevent It – Ansys
2. In-situ Investigation of the Onset of Cavitation Damage from Single Bubbles on Technical Alloys | Tribology Letters – SpringerLink
The Cavitation Process:
- Pressure Reduction: As a liquid flows through a system, the pressure can decrease in certain areas, such as the suction side of a pump impeller. 1. How Does Pump Suction Limit the Flow? www.pumpsandsystems.com
- Bubble Formation: When the pressure drops below the liquid’s vapor pressure, vapor bubbles form within the liquid. 1. Suction pressure falling below vapor pressure causes bubble formation [3]. – ResearchGate www.researchgate.net
- Bubble Collapse: As the liquid moves to a region of higher pressure, the vapor bubbles collapse violently. 1. Cavitation in industrial pumps: understand this phenomenon – Dynamox dynamox.net
- Damage: The collapse of these bubbles generates shock waves that can erode and damage the solid surface. 1. Modeling of shock wave produced by collapse of cavitation bubble using a fully conservative multiphase model – AIP Publishing pubs.aip.org
Effects of Cavitation Damage:
Opens in a new windowfluidhandlingpro.com cavitation damage
- Material Loss: Cavitation can cause pitting and erosion of metal surfaces. 1. Cavitation Erosion Characteristics for Different Metal Surface and Influencing Factors in Water Flowing System – MDPI www.mdpi.com
- Noise and Vibration: The collapse of bubbles generates noise and vibration, which can lead to fatigue and component failure. 1. Cavitation – Wikipedia en.wikipedia.org
- Reduced Efficiency: In pumps and turbines, cavitation can reduce efficiency and performance. 1. What is Pump Cavitation and How to Prevent It – Ansys www.ansys.com
- Component Failure: Severe cavitation damage can lead to the complete failure of components. 1. Cavitation: Causes, Damage & Prevention | Vaia www.vaia.com
To prevent cavitation damage, it’s essential to design and operate fluid systems to avoid conditions that lead to the formation and collapse of vapor bubbles.
Erosion Damage in Marine Engineering
Erosion damage in marine engineering refers to the gradual wearing away of a material’s surface due to the abrasive action of a fluid. In the marine environment, this typically involves the action of seawater against the hull, propellers, and other submerged components.
Factors contributing to erosion damage:
- Water velocity: Higher water velocity increases the erosive force. 1. Effect of Velocity on Erosion Rates | Download Scientific Diagram – ResearchGate www.researchgate.net
- Suspended solids: Particles in the water, such as sand, silt, or algae, act as abrasives.
- Cavitation: The formation and collapse of vapor bubbles in the water can cause localized erosion. 1. What is the Cavitation Phenomenon? – De Lorenzo SPA delorenzoglobal.com
- Material properties: The hardness and resistance to abrasion of the material determine its susceptibility to erosion.
Effects of erosion damage:
- Reduced component life: Erosion can lead to premature failure of components.
- Increased maintenance costs: Repair or replacement of eroded components is expensive.
- Reduced efficiency: Erosion can affect the performance of equipment, such as pumps and propellers. 1. Erosion of the propeller tips | Download Scientific Diagram – ResearchGate www.researchgate.net
- Safety risks: Severe erosion can compromise the structural integrity of components, leading to safety hazards.
To mitigate erosion damage, engineers often use materials with high abrasion resistance, implement protective coatings, and optimize fluid flow designs.
Stress Corrosion Cracking
Stress corrosion cracking (SCC) is a form of failure that occurs when a metal is subjected to tensile stress in a corrosive environment. It’s a combination of both mechanical stress and chemical attack.
1. Stress Corrosion Cracking (SCC) – AMPP
2. Stress corrosion cracking – MIT Energy Initiative
Process:
- Stress Concentration: Tensile stresses, often at points of stress concentration (like welds, holes, or notches), weaken the metal. 1. Stress Corrosion Cracking of Stainless Steel in Marine Environments – Warren Forensics www.warrenforensics.com
- Corrosive Environment: The corrosive environment (e.g., seawater) attacks the metal, creating tiny cracks. 1. Stress Corrosion Cracking: Mechanism & Chloride Effect – Vaia www.vaia.com
- Crack Propagation: The combination of stress and corrosion causes the cracks to grow slowly and unpredictably. 1. Stress Corrosion Cracking of Stainless Steel in Marine Environments – Warren Forensics www.warrenforensics.com
- Failure: Over time, the cracks can propagate to a critical size, leading to sudden and catastrophic failure. 1. Stress Corrosion Cracking of Stainless Steel in Marine Environments – Warren Forensics www.warrenforensics.com
Factors Affecting Stress Corrosion Cracking:
- Material susceptibility: Certain metals and alloys are more prone to SCC. 1. Stress Corrosion Cracking – What Factors Cause and Prevent It? – The Welding Institute theweldinginstitute.com
- Stress level: Higher tensile stress increases the risk of SCC.
- Corrosive environment: The presence of specific ions (e.g., chlorides) can accelerate SCC.
- Temperature: Elevated temperatures can increase the rate of SCC.
Preventing stress corrosion cracking involves careful material selection, stress reduction, environmental control, and regular inspection.
1. Mitigating the Risk Factors for Stress Corrosion Cracking – Unified Alloys
Atmospheric Corrosion in Marine Engineering
Atmospheric corrosion is the deterioration of a metal due to its exposure to the atmosphere. In marine environments, this corrosion is accelerated due to the presence of salt, moisture, and other corrosive substances.
Factors Affecting Atmospheric Corrosion:
- Salt Spray: The deposition of salt on metal surfaces creates a corrosive environment.
- Humidity: High humidity levels promote the formation of corrosive films on the metal surface.
- Temperature: Higher temperatures accelerate corrosion reactions.
- Pollutants: Industrial pollutants, such as sulfur oxides and nitrogen oxides, can contribute to corrosion.
Types of Corrosion:
- General Corrosion: Uniform attack on the entire metal surface.
- Pitting Corrosion: Localized attack resulting in the formation of pits.
- Crevice Corrosion: Corrosion occurring in confined spaces, such as under gaskets or washers.
Effects of Atmospheric Corrosion:
- Weakened structures: Corrosion reduces the strength and integrity of metal components.
- Increased maintenance costs: Frequent repairs and replacements are necessary.
- Safety risks: Severe corrosion can lead to structural failures and safety hazards.
To mitigate atmospheric corrosion, various protection methods, such as coatings, inhibitors, and cathodic protection, can be employed.