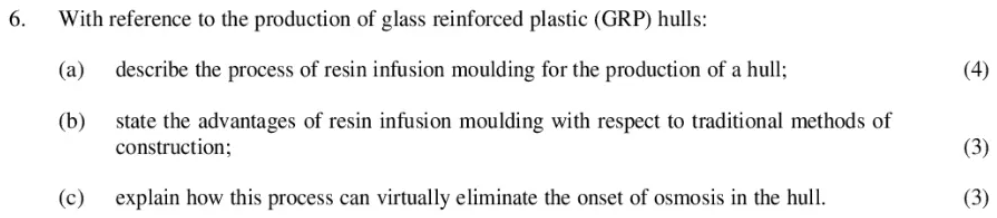
With reference to the production of glass reinforced plastic (GRP) hulls:
(a) describe the process of resin infusion moulding for the production of a hull;(4)
(b) state the advantages of resin infusion moulding with respect to traditional methods of construction;(3)
(c) explain how this process can virtually eliminate the onset of osmosis in the hull.(3)
Resin Infusion Molding for Hull Production
Resin infusion is a manufacturing process that produces high-quality composite parts with excellent mechanical properties. It’s widely used in the marine industry for hull construction.
Process Overview
- Mold Preparation: The mold, typically made from wood or metal, is prepared with a release agent to prevent the cured resin from adhering to it.
- Reinforcement Placement: Dry reinforcement layers (glass fiber, carbon fiber, etc.) are placed in the mold to form the desired shape and thickness.
- Vacuum Bagging: A flexible vacuum bag is placed over the reinforcement, creating a sealed environment.
- Resin Introduction: Liquid resin is introduced into the mold through a distribution system.
- Vacuum Application: A vacuum is applied to the bag, drawing the resin through the reinforcement and removing air bubbles.
- Curing: The resin cures under vacuum, resulting in a high-quality composite part.
Advantages of Resin Infusion:
- Improved fiber volume fraction: Higher percentage of fibers compared to hand lay-up.
- Consistent resin distribution: Ensures uniform properties throughout the part.
- Reduced void content: Vacuum removes air bubbles, improving mechanical properties.
- Lower styrene emissions: Reduced resin waste and environmental impact.
- Better surface finish: Produces a smoother and more consistent surface.
Challenges of Resin Infusion:
- Equipment and expertise: Requires specialized equipment and skilled operators.
- Molding complexity: Complex shapes can be challenging to infuse.
- Cycle time: The process can be slower than some other methods.
Overall, resin infusion is a valuable technique for producing high-quality GRP hulls with improved mechanical properties and reduced environmental impact.
Opens in a new windowwww.buschvacuum.com
resin infusion process for hull production
Other Traditional Methods of GRP Hull Construction
While resin infusion has gained popularity for its efficiency and quality, there are other traditional methods of constructing GRP hulls:
Hand Lay-Up
- Process: Resin is manually applied to the reinforcement, which is placed in a mold layer by layer.
- Advantages: Versatility for complex shapes, relatively low initial investment.
- Disadvantages: Labor-intensive, inconsistent fiber distribution, higher resin consumption.
Spray-Up
- Process: Resin and chopped glass fibers are sprayed onto the mold using specialized equipment.
- Advantages: Faster production, thicker sections achievable.
- Disadvantages: Higher resin consumption, potential for voids, and less control over fiber orientation.
Vacuum Bagging
- Process: Similar to resin infusion but without vacuum assistance.
- Advantages: Simpler setup than full resin infusion, good fiber volume fraction.
- Disadvantages: Potential for voids and slower curing time.
These methods, while not as efficient or controlled as resin infusion, are still used in certain applications, especially for smaller or custom-built vessels.
Advantages of resin infusion moulding with respect to traditional methods of construction
Resin infusion molding offers several advantages over traditional methods like hand lay-up and spray-up for GRP hull construction:
- Improved fiber volume fraction: Resin infusion results in a higher percentage of fibers in the composite, leading to increased strength and stiffness.
- Consistent resin distribution: The vacuum-assisted process ensures even resin distribution, preventing voids and weak spots.
- Reduced void content: The vacuum draws out air bubbles, creating a denser and stronger composite.
- Lower resin consumption: Less resin is wasted compared to hand lay-up or spray-up methods.
- Better surface finish: The infusion process typically produces a smoother and more consistent surface finish.
- Improved mechanical properties: The combination of higher fiber volume fraction and reduced voids leads to enhanced strength, stiffness, and impact resistance.
- Environmental benefits: Lower styrene emissions due to reduced resin waste.
These advantages contribute to the production of higher quality GRP components with improved performance and durability.
Applications of Resin Infusion in the Marine Industry
Resin infusion has become increasingly popular in the marine industry due to its numerous advantages. Here are some key applications:
- Hull Construction: The primary application, resin infusion produces high-quality, strong, and lightweight hulls for various boat types, from small recreational boats to larger commercial vessels.
- Decks and Superstructures: Large deck components and superstructures can be efficiently manufactured using resin infusion, offering improved strength and durability.
- Structural Components: Components like bulkheads, stringers, and frames can be produced with consistent quality and high strength-to-weight ratios.
- Marine Equipment: Resin infusion is used to manufacture various marine equipment, including tanks, hatches, and consoles.
Key benefits in these applications include improved mechanical properties, reduced weight, and enhanced durability compared to traditional methods.
Resin Infusion Molding and Osmosis Prevention
Resin infusion molding plays a crucial role in virtually eliminating the onset of osmosis in GRP hulls. Here’s how:
- Reduced Void Content: The vacuum-assisted process in resin infusion effectively removes air bubbles from the laminate, creating a denser and more compact structure. This minimizes potential voids where water can penetrate.
- Improved Resin Distribution: Resin is evenly distributed throughout the reinforcement, ensuring complete impregnation and reducing the likelihood of areas with resin-starved zones that are susceptible to water ingress.
- Higher Fiber Volume Fraction: A higher fiber-to-resin ratio in resin infusion creates a more robust and impermeable barrier against water penetration.
By addressing these factors, resin infusion significantly reduces the risk of osmosis, a common problem in traditionally constructed GRP hulls.