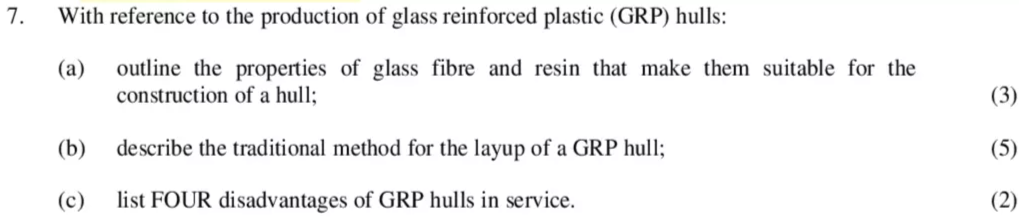
With reference to the production of glass reinforced plastic (GRP) hulls:
(a) outline the properties of glass fibre and resin that make them suitable for the construction of a hull;(3)
(b) describe the traditional method for the layup of a GRP hull;(5)
(c) list FOUR disadvantages of GRP hulls in service.(2)
Is glass reinforced plastic the same as fibreglass?
Yes, glass reinforced plastic (GRP) is the same as fiberglass.
1. What Is GRP? About Glass Reinforced Plastic
They are both terms used to describe a composite material made by combining a resin (usually a polymer) with glass fibers to create a strong, lightweight, and durable material.
1. What Is GRP? About Glass Reinforced Plastic | Gripclad
Fiberglass: Is a more common, general term referring to the material itself.
Glass reinforced plastic (GRP): Emphasizes the use of glass fibers as reinforcement. 1. What Is GRP? About Glass Reinforced Plastic | Gripclad gripclad.co.uk
General Properties of Glass Reinforced Plastic (GRP)
GRP, or fiberglass, is a composite material known for its versatility and desirable properties. Here are some of its key characteristics:
1. What Is GRP? | Glass Reinforced Plastic 101 – Evergrip
Key Properties of GRP:
- High strength-to-weight ratio: It’s strong and durable yet lightweight, making it ideal for various applications. 1. What Is GRP? | Glass Reinforced Plastic 101 – Evergrip evergrip.com
- Corrosion resistance: Resistant to a wide range of chemicals and atmospheric conditions. 1. What Is GRP? | Glass Reinforced Plastic 101 – Evergrip evergrip.com
- Electrical insulation: Non-conductive, making it suitable for electrical applications. 1. What Is GRP? | Glass Reinforced Plastic 101 – Evergrip evergrip.com
- Design flexibility: Can be molded into complex shapes. 1. Glass fiber reinforced plastic: definition and pros & cons – EuroPlas europlas.com.vn
- Durability: Resistant to wear and tear, offering a long lifespan. 1. GRP FAQs | GripClad UK gripclad.co.uk
- Cost-effective: Often provides a cost-effective alternative to traditional materials. 1. What Is GRP? About Glass Reinforced Plastic | Gripclad gripclad.co.uk
- Low maintenance: Generally requires minimal upkeep. 1. Top 10 benefits of GRP – HR Kilns hrfibreglass.co.uk
- Good thermal and acoustic insulation: Provides insulation against heat and noise. 1. Glass fibre-reinforced plastic vs. aluminium | insights by LAMILUX www.lamilux.com
Due to these properties, GRP has found widespread use in industries such as marine, automotive, construction, and electronics.
Properties of GRP Making it Suitable for Hull Construction
GRP, or fiberglass, is a popular choice for hull construction due to several key properties:
Buoyancy: GRP has inherent buoyancy, which can contribute to increased safety in case of hull damage.
High strength-to-weight ratio: GRP hulls are significantly lighter than those made from traditional materials like steel, leading to improved fuel efficiency and increased payload capacity.
Corrosion resistance: GRP is highly resistant to corrosion, eliminating the need for extensive maintenance and ensuring the hull’s longevity.
Design flexibility: GRP can be molded into complex shapes, allowing for optimized hull designs for different vessel types.
Insulation: GRP provides good thermal and acoustic insulation, improving passenger comfort and reducing noise levels.
Cost-effective: In many cases, GRP hulls can be more cost-effective to produce compared to traditional materials.
While GRP offers numerous advantages, it’s essential to consider its limitations, such as potential damage from impacts and the need for proper reinforcement in certain areas, when designing a hull.
Challenges of Using GRP for Hull Construction
While GRP offers numerous advantages for hull construction, it also presents certain challenges:
- Impact Resistance: While GRP is strong, it can be susceptible to impact damage, especially from underwater objects. Proper design and reinforcement are essential to mitigate this risk.
- Osmosis: Over time, water can penetrate the GRP laminate, leading to osmotic blistering. Modern resins and barrier coatings have significantly reduced this issue, but it remains a concern for older vessels.
- Repair and Maintenance: Repairing GRP can be more complex than metal hulls, requiring specialized knowledge and materials.
- Fatigue: Prolonged exposure to cyclic loading, such as wave action, can cause fatigue cracks in GRP, necessitating regular inspections.
- Thermal Expansion: GRP has a higher coefficient of thermal expansion compared to metals, which can lead to dimensional changes and potential stress.
Despite these challenges, advancements in GRP technology and construction techniques have significantly improved the material’s performance and durability in marine applications.
Traditional Hand Lay-Up Method for GRP Hulls
The traditional method for laying up a GRP hull is known as hand lay-up. This labor-intensive process involves manually applying resin and reinforcement to a mold to create the desired shape.
Steps Involved:
- Mold Preparation: The mold, typically made from wood or metal, is prepared with a release agent to prevent the cured resin from adhering to it.
- Reinforcement Placement: Glass fiber reinforcement, usually in the form of woven or chopped strands, is cut and placed in the mold to form the desired shape and thickness of the laminate.
- Resin Application: A catalyzed resin is applied to the reinforcement using brushes or rollers. The resin impregnates the fibers, bonding them together.
- Rollers and Bubbles: A roller is used to remove air bubbles from the laminate and ensure proper resin distribution.
- Layering: Multiple layers of reinforcement and resin are applied to achieve the required thickness and strength.
- Curing: The laminate is allowed to cure at room temperature or in a controlled environment, depending on the resin type.
- Finishing: Once cured, the hull is removed from the mold and any imperfections are corrected.
Key Considerations:
- Labor Intensive: Hand lay-up is time-consuming and requires skilled labor.
- Resin Waste: Some resin waste is inevitable due to the manual application process.
- Fiber Orientation: Careful attention must be paid to fiber orientation to optimize strength and stiffness.
- Thickness Control: Achieving consistent thickness can be challenging without automated equipment.
While this method is labor-intensive, it offers flexibility in terms of shape and design, making it suitable for smaller production runs and custom hulls.
Other GRP Hull Construction Methods
While hand lay-up is a traditional method, several other techniques have been developed to improve efficiency, quality, and consistency in GRP hull construction.
Spray-Up Method
- Process: Resin and chopped glass fibers are sprayed onto the mold using specialized equipment.
- Advantages: Faster production, thicker sections achievable, and better fiber distribution.
- Disadvantages: Higher resin consumption, potential for voids, and less control over fiber orientation.
Resin Infusion
- Process: Dry reinforcement is placed in the mold, and resin is infused under vacuum to remove air and ensure complete impregnation.
- Advantages: Improved fiber volume fraction, reduced resin waste, and better mechanical properties.
- Disadvantages: Requires specialized equipment and careful process control.
Vacuum Bagging
- Process: Similar to resin infusion but without vacuum assistance.
- Advantages: Simpler setup than full resin infusion, good fiber volume fraction.
- Disadvantages: Potential for voids and slower curing time.
RTM (Resin Transfer Molding)
- Process: Resin is injected into a closed mold filled with dry reinforcement.
- Advantages: High-quality finish, precise control over fiber orientation, and good mechanical properties.
- Disadvantages: Requires complex tooling and high initial investment.
Each method has its own advantages and disadvantages, and the choice of method depends on factors such as hull size, desired quality, production volume, and cost.
Disadvantages of GRP Hulls in Service
While GRP hulls offer many advantages, they also have some inherent limitations:
- Impact Resistance: GRP, while strong, is less resistant to impact compared to steel or aluminum. A hard collision can cause significant damage.
- Osmosis: The process where water penetrates the laminate can lead to blistering and delamination, reducing the hull’s structural integrity. Modern resins and barrier coatings have significantly mitigated this issue.
- Fatigue: Prolonged exposure to cyclic loading, such as wave action, can cause fatigue cracks in the GRP laminate, requiring regular inspections and maintenance.
- Repair Challenges: Repairing GRP damage can be more complex and time-consuming than repairing metal hulls, requiring specialized skills and materials.
- Thermal Expansion: GRP has a higher coefficient of thermal expansion than metals, which can lead to dimensional changes and potential stress.
- Limited Thickness: Achieving the same level of stiffness as a metal hull often requires thicker GRP laminates, which can increase weight and cost.
It’s important to note that many of these challenges have been addressed through advancements in GRP technology and construction methods, making the material a viable option for a wide range of marine applications.