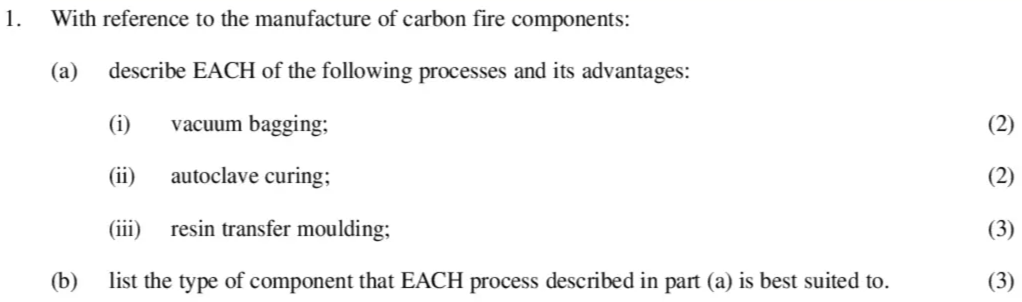
Three different composite fabrication processes: vacuum bagging, autoclave curing, and resin transfer molding (RTM). Each process has its own advantages and disadvantages, and is best suited for different types of components.
Here’s a breakdown of each process:
Vacuum bagging:
Process: A dry fiber preform is placed in a mold, and then covered with a vacuum bag. The air is evacuated from the bag, which applies pressure to the preform and forces the resin to flow through it. The part is then cured under heat.
- Advantages:
- Simple and relatively inexpensive process.
- Can be used with a wide variety of mold materials and shapes.
- Good for producing parts with a high fiber volume fraction.
- Disadvantages:
- Limited to parts with simple geometries.
- Voiding (air pockets) can be an issue.
- Not suitable for high-performance applications.
Autoclave curing:
- Process: The vacuum-bagged part is placed in an autoclave, which is a pressure vessel that can be heated and pressurized. The pressure helps to consolidate the laminate and eliminate voids.
- Advantages:
- Produces high-quality parts with excellent surface finish and low void content.
- Suitable for complex geometries and high-performance applications.
- Disadvantages:
- Expensive process due to the high cost of autoclaves.
- Limited throughput due to the long cycle times.
- Not suitable for large parts.
Resin transfer molding (RTM):
- Process: The dry fiber preform is placed in a closed mold, and then resin is injected into the mold under pressure. The part is then cured under heat.
- Advantages:
- Can produce high-quality parts with good surface finish and low void content.
- Faster cycle times than autoclave curing.
- Can be used for larger parts than vacuum bagging.
- Disadvantages:
- More complex process than vacuum bagging.
- Requires specialized molds and equipment.
- Not suitable for all geometries.