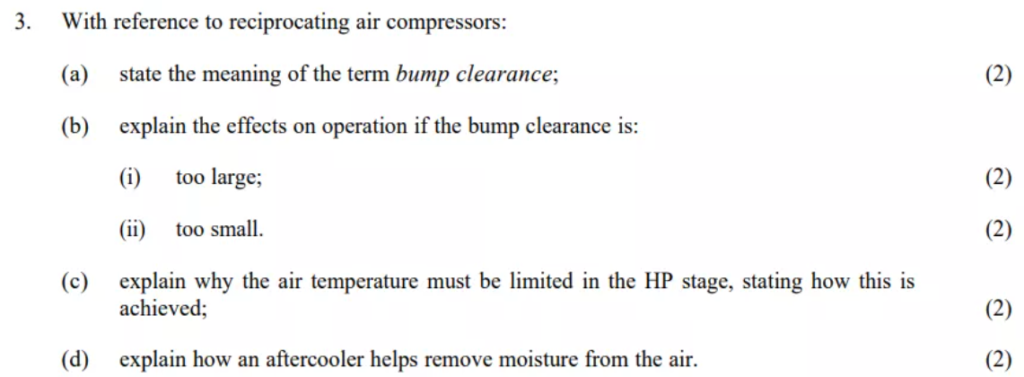
With reference to reciprocating air compressors:
(a) state the meaning of the term bump clearance;(2)
(b) explain the effects on operation if the bump clearance is:
(i) too large;(2)
(ii) too small.(2)
(c) explain why the air temperature must be limited in the HP stage, stating how this is achieved;(2)
(d) explain how an aftercooler helps remove moisture from the air.(2)
Question 3. Overall poor answers. Several have no understanding of the importance of bump clearance or the safety aspects of intercooling.
Reciprocating air compressor
A reciprocating air compressor is a type of positive displacement compressor that uses pistons driven by a crankshaft to deliver gases, typically air, at high pressure. It operates on the principle of reciprocation, where the piston moves back and forth within a cylinder, compressing the air trapped inside.
1. Reciprocating compressor – Wikipedia
2. Reciprocating and Rotary Compressor: What’s the Difference – Atlas Copco Slovenia
Key Components and Working Principle:
- Cylinder and Piston:
- The core of the compressor is a cylinder containing a piston that moves back and forth within it. 1. The basics of a piston or reciprocating compressor – Atlas Copco UK www.atlascopco.com
- Crankshaft and Connecting Rod:
- The piston is connected to a crankshaft via a connecting rod. 1. Crankshaft – Wikipedia en.wikipedia.org
- The rotating crankshaft converts rotary motion from a motor or engine into the reciprocating motion of the piston.
- Inlet and Outlet Valves:
- The cylinder head houses inlet and outlet valves, which are typically spring-loaded and open and close based on pressure differences.
- Compression Cycle:
- Intake Stroke:
- The piston moves downward, creating a vacuum in the cylinder. 1. The basics of a piston or reciprocating compressor – Atlas Copco Magyarország www.atlascopco.com
- The inlet valve opens, allowing air to be drawn into the cylinder. 1. Understanding Reciprocating Compressors | Air to Air Engineering airtoair.com.my
- Compression Stroke:
- The piston moves upward, compressing the air trapped in the cylinder. 1. Previous Page www.chm.bris.ac.uk
- Both valves are closed during this stroke. 1. What is a reciprocating air compressor? – Industrial Air Systems NZ www.industrialair.co.nz
- Discharge Stroke:
- The compressed air reaches the desired pressure, the outlet valve opens. 1. Reciprocating Compressor Basics roteckcompressor.com
- The piston continues its upward movement, pushing the compressed air out of the cylinder and into the discharge line. 1. Piston compressors: How they work – Air Compressors – Air treatment – ALUP Global www.alup.com
- Intake Stroke:
Types of Reciprocating Air Compressors:
- Single-Stage: Air is compressed in one cylinder to the final pressure.
- Multi-Stage: Air is compressed in multiple stages using several cylinders with progressively smaller volumes, achieving higher final pressures.
- Oil-Lubricated: Oil is used for lubrication and sealing, offering better cooling and efficiency.
- Oil-Free: No oil is used in the compression chamber, producing cleaner air but might have slightly lower efficiency.
Advantages:
- High Pressure Capability: Can deliver compressed air at high pressures, suitable for various industrial and marine applications. 1. Guide to Reciprocating Compressors – Atlas Copco Greece www.atlascopco.com
- Efficiency at Varying Loads: Maintains relatively good efficiency even at partial loads.
- Long Service Life: With proper maintenance, they can have a long service life. 1. How to Extend Your Air Compressor Life Expectancy – Fluid-Aire Dynamics fluidairedynamics.com
Disadvantages:
- Pulsating Flow: The flow of compressed air is pulsating due to the reciprocating motion of the piston. Pulsation dampers may be required to smooth the flow.
- Higher Noise and Vibration: They tend to generate more noise and vibration than other compressor types like rotary screw compressors. 1. Reciprocating and Rotary Compressor: What’s the Difference – Atlas Copco UAE www.atlascopco.com
- More Maintenance: The presence of moving parts and valves requires regular maintenance to ensure proper operation and prevent wear and tear.
Applications on Marine Vessels:
- Starting Air: Providing high-pressure air for starting main and auxiliary engines.
- Control Air: Supplying air for pneumatic control systems, such as valves, actuators, and other instrumentation.
- Service Air: Used for general purposes like cleaning, pneumatic tools, and other onboard applications.
In essence: A reciprocating air compressor is a reliable and versatile machine capable of delivering compressed air at various pressures for diverse applications on a vessel. Its positive displacement action, high-pressure capability, and good efficiency under varying loads make it a valuable asset in the marine industry.
Bump clearance
In the context of a reciprocating air compressor, bump clearance refers to the minimum distance or gap between the top of the piston (when it’s at its highest point in the cylinder, known as Top Dead Center or TDC) and the cylinder head.
Why is it important?
- Prevents Damage: The bump clearance is essential to prevent the piston from physically striking the cylinder head during operation. Such contact would cause severe damage to both components.
- Affects Volumetric Efficiency: The clearance volume directly influences the compressor’s volumetric efficiency. A larger clearance volume means more compressed air remains in the cylinder after the discharge stroke, reducing the amount of fresh air that can be drawn in on the next intake stroke. This leads to lower compressor output and efficiency.
Ideal Bump Clearance:
The bump clearance should be:
- As small as practically possible: To maximize volumetric efficiency and compressor output.
- But not too small: To avoid the risk of the piston hitting the cylinder head due to thermal expansion or slight misalignment.
Factors Affecting Bump Clearance:
- Wear and Tear: Over time, wear on the piston, rings, and bearings can increase the bump clearance.
- Thermal Expansion: Components expand when heated, potentially reducing the clearance.
- Manufacturing Tolerances: Slight variations in manufacturing can affect the initial clearance.
Checking and Adjusting:
- Regular checks: Bump clearance should be checked periodically as part of the compressor’s maintenance routine.
- Adjustment: If the clearance is outside the specified tolerance, it can be adjusted by adding or removing shims from the connecting rod bearings or by machining the piston or cylinder head.
Consequences of Incorrect Bump Clearance:
- Too Small:
- Piston hitting the cylinder head, causing severe damage.
- Increased noise and vibration.
- Reduced compressor efficiency.
- Too Large:
- Reduced volumetric efficiency and compressor output.
- Increased running time and energy consumption to achieve the desired air delivery.
In summary, bump clearance is a critical parameter in reciprocating compressors, influencing both their safety and efficiency. It’s vital to maintain the correct clearance through regular checks and adjustments to ensure optimal compressor performance and avoid costly damage.
Bump Clearance Too Large/Too Small
Bump Clearance Too Large
- Reduced Volumetric Efficiency:
- Residual Air: A larger bump clearance means a greater volume of high-pressure air remains in the cylinder after the discharge stroke.
- Re-expansion: This trapped air expands during the beginning of the suction stroke, occupying space that could otherwise be filled with fresh air.
- Less Intake: The compressor draws in less air on each intake stroke, reducing its overall output capacity and volumetric efficiency.
- Longer Running Time: The compressor has to run for a longer duration to deliver the same volume of compressed air, leading to increased energy consumption and wear on the machine.
- Mechanical Stress:
- Delayed Valve Closure: The expanding air in the clearance volume may delay the closing of the discharge valve, potentially causing it to flutter or slam shut, leading to increased wear and potential damage.
Bump Clearance Too Small
- Mechanical Damage:
- Piston-Cylinder Head Contact: The most severe consequence is the piston physically striking the cylinder head at Top Dead Center (TDC).
- Component Damage: This contact can cause severe damage to both the piston and the cylinder head, potentially leading to catastrophic failure of the compressor.
- Increased Noise and Vibration: Even if no direct contact occurs, a very small clearance can cause excessive noise and vibration as the piston approaches TDC.
- Overheating:
- Reduced Clearance Volume: A smaller clearance volume means less space for compressed air to expand during the suction stroke.
- Higher Compression Ratio: This effectively increases the compression ratio, leading to higher temperatures in the compressed air.
- Thermal Stress: The higher temperatures can cause thermal stress on the piston, valves, and other components, potentially leading to premature wear or failure.
- Reduced Efficiency:
- Leakage: If the clearance is too tight, it can hinder proper sealing between the piston rings and the cylinder wall, leading to leakage of compressed air back into the crankcase, reducing efficiency.
Ideal Bump Clearance:
The ideal bump clearance is a compromise between maximizing volumetric efficiency and ensuring mechanical safety. It’s typically specified as a percentage of the cylinder bore diameter, often in the range of 0.3% to 1%, depending on the compressor design and operating conditions.
Conclusion
Maintaining the correct bump clearance is essential for optimal compressor performance, efficiency, and longevity. Too large a clearance results in reduced output and increased energy consumption, while too small a clearance risks mechanical damage and overheating. Regular checks and adjustments are necessary to maintain the proper clearance and ensure the compressor operates safely and effectively.
Air temperature
In the HP (High Pressure) stage of a reciprocating air compressor, limiting the air temperature is crucial for several reasons:
1. Lubrication and Oil Degradation:
- Oil-Lubricated Compressors: In oil-lubricated compressors, excessive temperatures can lead to the breakdown of the lubricating oil, forming carbon deposits and sludge. This can clog valves, reduce efficiency, and increase wear on internal components.
- Autoignition: In extreme cases, very high temperatures can cause the lubricating oil to autoignite, leading to a potential fire or explosion hazard.
2. Material Limitations:
- Thermal Stress: High temperatures can cause thermal stress on the piston, cylinder head, valves, and other components. This stress can lead to material fatigue, warping, and eventual failure.
- Sealing Issues: High temperatures can degrade seals and gaskets, leading to air leaks and reduced compressor efficiency.
3. Efficiency and Performance:
- Reduced Volumetric Efficiency: High temperatures increase the volume of the compressed air, reducing the amount of fresh air that can be drawn in on the next intake stroke. This lowers the compressor’s volumetric efficiency and output. 1. Performance Assessment of Air Compressor | Calculation and Energy Conservation opportunities www.seaenergy.in
- Increased Energy Consumption: The compressor has to work harder to compress the hotter air, leading to increased energy consumption and operating costs.
How Air Temperature is Limited in the HP Stage:
Several methods are used to limit air temperature in the HP stage:
- Intercooling:
- Purpose: The most common method involves intercooling between stages of a multi-stage compressor. 1. Use of an intercooler in between the stages of a multi-stage compressor results in – Testbook testbook.com
- Process: The compressed air from the LP (Low Pressure) stage is passed through an intercooler, where it is cooled by circulating water or air. This reduces the temperature of the air before it enters the HP stage for further compression. 1. Understanding Air Compressor Intercooler Maintenance – FS-Elliott www.fs-elliott.com
- Water Injection:
- Purpose: In some cases, water is injected into the HP cylinder during the compression stroke.
- Process: The water evaporates, absorbing heat from the compressed air and lowering its temperature. This method is less common and requires careful control to avoid excessive moisture in the compressed air.
- Reduced Compression Ratio:
- Multi-Staging: Dividing the compression process into multiple stages with intercooling allows for lower compression ratios in each stage, reducing the temperature rise in each cylinder.
- Cylinder Design: The HP cylinder may be designed with a larger diameter or other features to reduce the compression ratio and limit temperature rise.
- Efficient Valve Design:
- Optimized Flow: Valves designed for efficient flow and minimal pressure drop help reduce heat generation during compression.
- Proper Maintenance:
- Cleanliness: Keeping the compressor and its components clean and free of debris helps ensure efficient heat transfer and prevents hot spots that could lead to localized overheating.
- Lubrication: Proper lubrication is essential for reducing friction and heat generation in the compressor.
Conclusion:
Limiting the air temperature in the HP stage of a reciprocating air compressor is essential for ensuring its safe, efficient, and reliable operation. By using techniques like intercooling, water injection, and optimized design, the temperature can be kept within safe limits, preventing lubrication issues, material damage, and performance degradation.
Remember that regular maintenance and adherence to manufacturer’s recommendations are also vital for maintaining the compressor’s health and preventing overheating.
Aftercooler
An aftercooler is a crucial component in compressed air systems, especially those supplying air for critical applications like control instrumentation.
It works on the principle of cooling the compressed air, causing the water vapor within it to condense into liquid water, which can then be easily removed from the system.
1. Unveiling the Power and Importance of Aftercoolers | RasMech
2. Benefits of an air compressor aftercooler – Atlas Copco India
How it works:
- Hot Compressed Air: Air leaving the compressor is typically hot due to the compression process. This hot air can hold a significant amount of water vapor. 1. What Does Summer Heat Do To Your Air Compressor? – Fluid-Aire Dynamics fluidairedynamics.com
- Cooling: The aftercooler utilizes either air or water as a cooling medium to reduce the temperature of the compressed air. 1. Aftercoolers vs. Intercoolers: What’s the Difference? – NiGen International nigen.com
- Condensation: As the air cools, its ability to hold water vapor decreases. The excess water vapor condenses into liquid water droplets. 1. All About Compressed Air Aftercoolers | VMAC Air Compressors www.vmacair.com
- Separation: The condensed water droplets are separated from the air stream using one or more of the following mechanisms:
- Gravity Separation: In some aftercoolers, the design incorporates baffles or chambers that allow the heavier water droplets to fall out of the air stream due to gravity.
- Centrifugal Separation: Cyclone separators or similar mechanisms create a swirling motion in the air stream, forcing the denser water droplets to the outer wall, where they collect and drain.
- Coalescing Filters: These filters use a fine mesh or other media to capture and coalesce the tiny water droplets into larger drops, which then fall due to gravity and are collected in a drain trap.
- Dry Air Discharge: The cooled and dried air, with significantly reduced moisture content, is then discharged from the aftercooler and ready for further filtration or use in pneumatic control systems.
Types of Aftercoolers:
- Air-Cooled Aftercooler: Uses ambient air blown across a finned heat exchanger to cool the compressed air. 1. Aftercooler | GSA – Global Standard Air/Gas www.gsadryer.com
- Water-Cooled Aftercooler: Utilizes a water-cooled heat exchanger, where cooling water flows through tubes or channels to remove heat from the compressed air. 1. The Importance of Cooling Compressed Air – Atlas Copco USA www.atlascopco.com
Benefits of Aftercoolers in Moisture Removal:
- Reduced Water Content: Aftercoolers significantly reduce the amount of water vapor in the compressed air, preventing condensation and associated problems in downstream equipment and piping. 1. Benefits of an air compressor aftercooler – Atlas Copco India www.atlascopco.com
- Corrosion Prevention: By removing moisture, aftercoolers help prevent corrosion in the compressed air system and connected pneumatic components. 1. Water-Cooled vs. Air-Cooled Aftercoolers – NiGen International nigen.com
- Improved Air Quality: Dry air is essential for the proper functioning of sensitive control instrumentation, as moisture can cause malfunctions, sticking valves, and inaccurate readings.
- Energy Savings: Removing moisture also increases the efficiency of the compressed air system, as dry air requires less energy to compress and transport.
In Summary:
Aftercoolers play a critical role in removing moisture from compressed air by cooling it, causing condensation, and separating the liquid water from the air stream. This process is vital for ensuring the quality and reliability of compressed air used for control instrumentation and other critical applications on a vessel.
1. All About Compressed Air Aftercoolers | VMAC Air Compressors