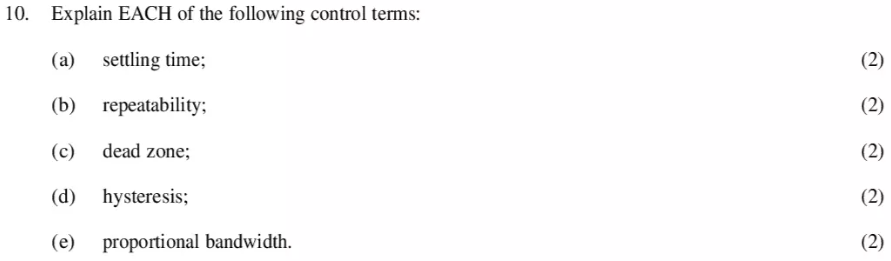
Explain EACH of the following control terms:
(a) settling time;(2)
(b) repeatability;(2)
(c) dead zone;(2)
(d) hysteresis;(2)
(e) proportional bandwidth.(2)
Settling Time in Control Systems
Settling time is a crucial performance metric in control systems that quantifies the time it takes for a system’s output to reach and stay within a specified tolerance band around its final value after a disturbance or setpoint change.
Key Points:
- Tolerance band: This is usually defined as a percentage of the final value, such as ±2% or ±5%.
- Final value: The steady-state value the system converges to after the transient response.
Visual Representation:
Opens in a new windowwww.chegg.com
system response with settling time indicated
Factors Affecting Settling Time:
- System damping: Underdamped systems tend to have longer settling times due to oscillations.
- System gain: High gains can lead to faster responses but also to overshoot and longer settling times.
- Noise and disturbances: External factors can influence settling time.
Importance of Settling Time:
- System stability: A shorter settling time indicates a more stable system.
- Performance evaluation: It’s a key parameter for comparing different control strategies.
- Design criteria: Settling time is often a design specification for control systems.
In essence, settling time is a measure of how quickly a system can recover from a disturbance and return to normal operation.
Repeatability in Control Systems
Repeatability in a control system refers to the ability of a system to consistently produce the same output for the same input conditions. In other words, it measures how closely the system can reproduce its results under identical operating conditions.
Key points:
- Consistency: The system should produce similar results across multiple trials.
- Reproducibility: The results should be obtainable by different operators or equipment.
- Accuracy: While repeatability is about consistency, accuracy refers to how close the output is to the desired value.
Factors affecting repeatability:
- System noise: Random fluctuations can impact repeatability.
- Sensor accuracy: Inaccurate sensors can lead to inconsistencies.
- Actuator precision: Variations in actuator performance can affect repeatability.
- Environmental conditions: Changes in temperature, humidity, or pressure can influence results.
Importance of repeatability:
- Process control: Consistent results are crucial for maintaining product quality.
- System reliability: A repeatable system is more predictable and reliable.
- Calibration: Repeatability is essential for accurate calibration of instruments.
In summary, repeatability is a measure of a system’s ability to deliver consistent performance under identical conditions.
Dead Zone in Control Systems
A dead zone in a control system is the range of input values for which there is no output response. In simpler terms, it’s a region around the setpoint where the system is insensitive to changes in the input.
Key characteristics:
- No output: There is no control action until the input value exceeds the dead zone.
- Hysteresis: Dead zone is often associated with hysteresis, which is the difference between the input values for increasing and decreasing outputs.
- Non-linearity: It introduces non-linearity into the system’s response.
Impact on system performance:
- Reduced sensitivity: The system becomes less responsive to small changes in the input.
- Steady-state error: Dead zone can contribute to steady-state error, as the system might not be able to reach the exact setpoint.
- Oscillations: In some cases, dead zone can lead to oscillations or hunting.
Example:
A thermostat with a dead zone of 2 degrees Celsius will not activate heating or cooling until the temperature deviates by more than 2 degrees from the setpoint.
Opens in a new windowwww.researchgate.net
dead zone in a control system
Understanding dead zone is crucial for designing and tuning control systems, as it can significantly affect system performance.
Hysteresis in Control Systems
Hysteresis in a control system refers to the difference between the input values required to initiate an action (increasing input) and the input values required to reverse the action (decreasing input). In simpler terms, it’s a lag or delay in the system’s response to changes in the input.
Key characteristics:
- Loop: The system follows a different path when the input is increasing compared to when it is decreasing.
- Non-linearity: Hysteresis introduces non-linearity into the system’s behavior.
- Energy dissipation: Hysteresis often involves energy loss, such as in mechanical systems due to friction.
Impact on system performance:
- Reduced sensitivity: The system becomes less responsive to small changes in the input.
- Oscillations: Hysteresis can contribute to oscillations or hunting in control systems.
- Accuracy: It can reduce the accuracy of the system’s output.
Example:
A thermostat with hysteresis might require a temperature to drop below a certain point before turning on the heating, and then require the temperature to rise above another point before turning it off.
Opens in a new windowwww.clippard.com
hysteresis loop in a control system
Understanding hysteresis is essential for designing and tuning control systems, as it can significantly affect system performance and stability.
Proportional Bandwidth in Control Systems
Proportional bandwidth is a term used in control systems to describe the range of input values over which a controller’s output changes from minimum to maximum. In simpler terms, it’s the span of error (difference between setpoint and process variable) within which the controller actively adjusts the control output.
Key points:
- Range of influence: It defines the range of error values that affect the controller’s output.
- Inversely related to gain: A wider proportional band corresponds to a lower proportional gain, and vice versa.
- Impact on control action: A narrow bandwidth results in a more aggressive control action, while a wider bandwidth leads to a more gentle response.
Visual representation:
Opens in a new windowwww.supersystems.com
proportional band in a control system
Importance of proportional bandwidth:
- Stability: A wider bandwidth generally improves stability but can lead to slower response.
- Offset: A narrow bandwidth can reduce offset but increase the risk of instability.
- Tuning: Proportional band is a key parameter in controller tuning.
In essence, proportional bandwidth determines the sensitivity of a controller to changes in the error signal.